底轮模锻毛坯工厂
模具是模锻工艺的关键部件,其设计和制造质量直接影响到产品的质量和生产效率。模具设计需要考虑以下因素:产品的形状和尺寸:模具的型腔必须与产品的形状和尺寸相匹配,以确保工件的成形精度。材料的选择:模具材料需要具有良好的耐高温、耐磨损和耐腐蚀性能,以确保模具的使用寿命和稳定性。模具结构:模具结构应合理、紧凑,易于加工和装配,以提高生产效率和降低其制造成本。在模具制造过程中,需要采用先进的加工设备和工艺,如数控加工、电火花加工、线切割等,以确保模具的精度和表面质量。同时,还需要对模具进行严格的检测和试模,以确保其符合设计要求。模锻过程中,模具的温度分布对金属的流动性和成形性有很大影响。底轮模锻毛坯工厂
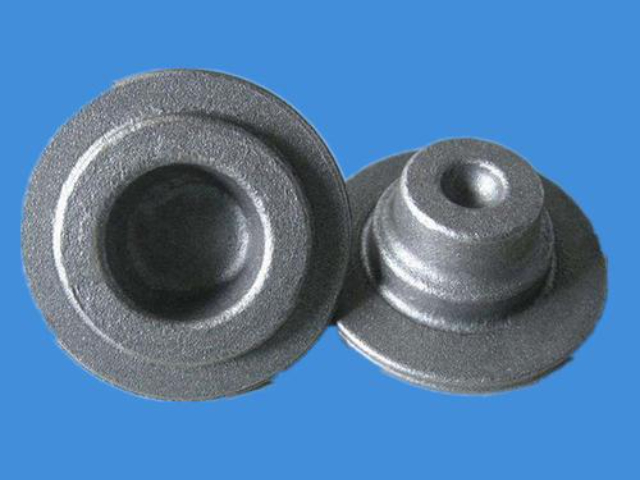
模锻工艺的产品具有一系列特点和优势,这些特点使得模锻件在多个领域得到广泛应用。以下是关于模锻工艺产品的详细回答:产品特点:高精度:模锻件利用模具锻出,因此其精度要求较高,且能锻出结构复杂的产品。高效率:模锻时,金属在型槽内变形,成形速度快,生产率高,适合成批、大量生产。高质量:模锻件表面质量较好,加工余量较小,可以节省金属材料,切削加工量少。强度高:模锻工艺能使金属流线分布更为合理、组织更加致密,从而提高零件的力学性能。不锈钢模锻加工生产供应商模锻件的生产周期较短,适合大批量生产。
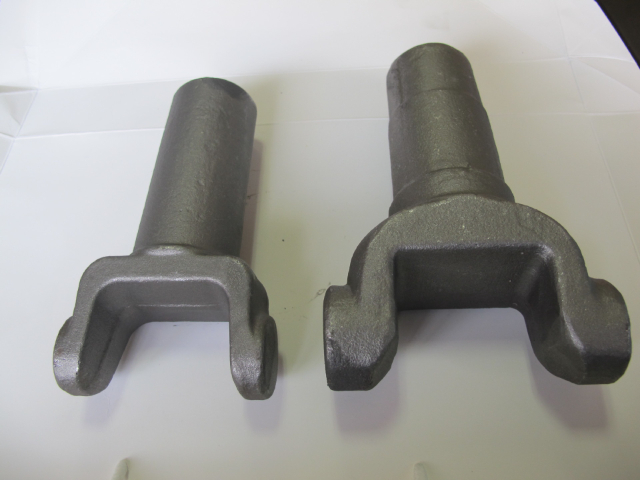
当前,我国模锻件年产量虽已先于日本、德国等发达国家,但资源消耗与浪费问题不容忽视。为提升行业可持续性,我们亟需强化模锻生产中的节能、节材及环保措施。具体而言,推广闭式模锻技术是关键一步,该技术通过封闭模膛成形,有效避免了开式模锻中沿分模面产生的横向飞边,不仅提升了材料利用率,还明显改善了锻件的几何精度、表面质量,并降低了能耗。此外,推动整体精锻技术的应用亦是重要方向。相较于传统的分体制造后铆接、焊接或螺栓连接的方式,整体精锻以厚板、厚壁管为坯料,通过精密锻造工艺实现一体化成形,不仅大幅度减轻了产品重量,更在性能上实现了质的飞跃,如发动机飞轮托盘与悬挂系统支架等部件的制造便因此受益。这一转变不仅符合轻量化制造的全球趋势,更是对资源高效利用与环境保护理念的深入实践。
随着工业技术的不断进步和市场需求的变化,模锻工艺也在不断发展和创新。未来模锻工艺的发展趋势主要包括以下几个方面:精密化:随着对零部件精度要求的不断提高,模锻工艺将向更加精密化的方向发展。通过优化模具设计、改进工艺参数等手段提高锻件的精度和表面质量。自动化:自动化是模锻工艺发展的重要方向之一。通过引入自动化设备和控制系统实现模锻工艺的自动化生产降低人工成本提高生产效率。智能化:随着人工智能技术的不断发展模锻工艺将向智能化方向发展。通过引入智能传感器、大数据分析等技术手段实现模锻工艺的智能控制和优化提高生产效率和产品质量。绿色化:绿色制造是当前制造业的重要发展趋势之一。模锻工艺也将向绿色化方向发展通过优化工艺参数、采用环保材料等手段降低能耗和减少环境污染实现可持续发展。模锻件的壁厚应均匀一致,避免出现厚薄不均的情况。

作为一种常见的模锻设备,平锻机在生产过程中可能会遇到一些问题,如杆部长度不稳、直线度超差、折叠、错模等。针对这些问题,可以采取以下解决措施:杆部长度不稳、直线度超差:定期检查上滑块压力,确保压力稳定;调整模具和夹紧机构,确保坯料在锻造过程中保持稳定的长度和直线度。折叠:调整模具和冲头位置,确保它们在锻造过程中处于同一中心线上;检查并更换磨损的模具和夹紧机构部件,防止因夹紧力不足导致的折叠现象。错模:调整夹持器高度和安装误差,确保冲头和凹模在锻造过程中能够准确对位;定期检查和维护模具和夹紧机构部件的精度和稳定性。模锻件的表面粗糙度对零件的摩擦、磨损和密封性能有影响。齿坯模锻毛坯单位
模锻过程中产生的废料可以通过回收再利用,降低生产成本。底轮模锻毛坯工厂
在航空航天领域,模锻工艺同样发挥着重要作用。航空航天器对零部件的性能要求极高,需要承受极端的温度和压力条件,同时还需要具备良好的抗疲劳性和耐腐蚀性。模锻工艺能够生产出强度高、精度高、性能高的锻件,满足航空航天领域对零部件的苛刻要求。例如,飞机发动机中的转子、涡轮叶片、机身构件等关键部件,都采用了模锻工艺进行生产。这些部件不仅具有优异的力学性能,还能够在极端环境下保持稳定的运行状态,为航空航天器的安全飞行提供了有力保障。底轮模锻毛坯工厂
上一篇: 合金钢锻造锻件加工企业
下一篇: 喷嘴锻打企业