面轮热锻毛坯公司
在热锻加工过程中,温度控制是关键环节之一,直接关系到锻件的成型质量、组织性能及后续加工性能。原材料需根据材料特性和锻造工艺要求,在加热炉中加热至适当的温度范围。过高的温度会导致材料晶粒粗大、氧化严重,甚至出现过烧现象;而过低的温度则会影响材料的塑性和变形抗力,增加锻造难度。因此,精确控制加热温度至关重要。同时,还需注意加热的均匀性,确保材料内外温度一致,避免出现局部过热或过冷导致的应力集中和裂纹等问题。为实现这一目标,可采用多段加热、保温时间控制、炉内气流循环等措施,以提高加热效率和均匀性。热锻技术不仅提升了木地板的物理性能,还赋予了其更高的艺术价值和审美享受。面轮热锻毛坯公司
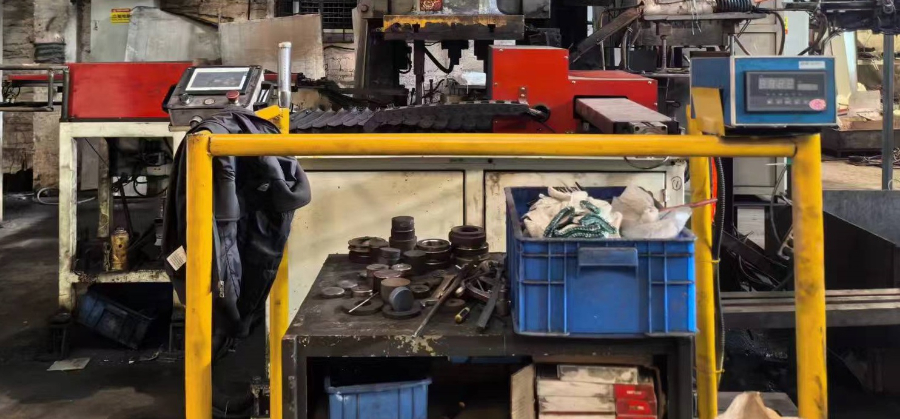
热锻加工过程中,需要注意以下几点以确保加工质量和安全性:温度控制:加热温度是热锻成功的关键。需确保材料均匀加热至合适的温度范围,一般在再结晶温度以上,但避免过热导致晶粒粗化或材料性能下降。同时,在加热过程中要注意翻动工件,以保证加热均匀。模具设计与选用:模具的设计需充分考虑工件的形状、尺寸和精度要求,以及材料的热物理性能。模具材料应具有良好的耐高温、耐磨损和耐冲击性能。在选用模具时,还需考虑其冷却系统,以控制模具温度,延长使用寿命。锻造工艺参数:包括锻造压力、速度、变形量等参数的设定需合理。过大的锻造压力或速度可能导致工件开裂或模具损坏,而过小的变形量则可能影响工件的内部组织结构和性能。安全检查与防护:热锻过程中涉及高温、高压等危险因素,需定期进行设备安全检查,确保防护装置完好。操作人员需穿戴好防护用品,如高温手套、防护眼镜等,以避免烫伤等伤害。冷却与后续处理:锻造后的工件需合理冷却,避免过快或过慢导致组织应力集中或产生裂纹。后续还需进行热处理、表面处理等工艺,以进一步改善工件的性能和外观质量。底轮热锻厂家结合热锻与热处理技术,可以精细控制木地板的含水率,预防因湿度变化引起的膨胀或收缩。
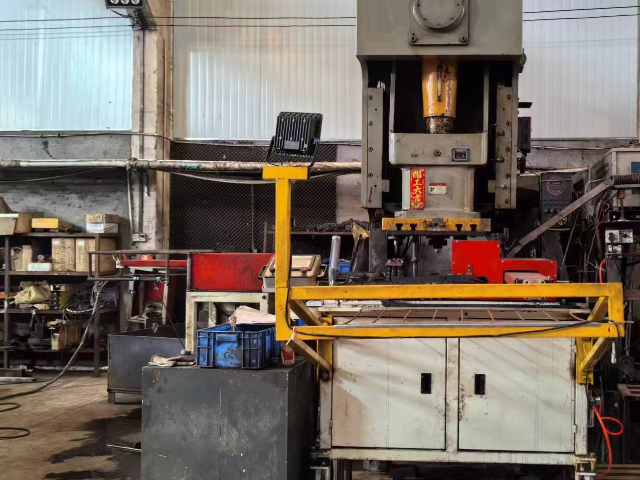
铝合金热锻,作为一种先进的金属成形工艺,其基本原理在于利用高温下铝合金材料的良好塑性和流动性,通过模具的施压作用,使金属坯料发生塑性变形,从而获得所需形状、尺寸和性能的锻件。相较于冷加工,热锻能够在较低的压力下实现复杂形状的成形,同时有效减少材料的加工硬化和裂纹倾向,提高锻件的内在质量和机械性能。铝合金在加热过程中,其内部原子活动加剧,有助于消除铸造缺陷,如缩孔、疏松等,并通过动态再结晶细化晶粒,进一步提升材料的强度和韧性。此外,热锻还能提高材料的致密度和表面光洁度,为后续加工处理(如机加工、热处理)打下良好基础,广泛应用于航空航天、汽车制造、船舶工业等领域,成为高级装备制造中不可或缺的一环。
热锻工艺之所以在金属加工领域占据重要地位,得益于其高效性和灵活性。在高温条件下,金属材料的变形抗力明显降低,使得锻造过程可以在较小的力量下完成,从而提高了生产效率。此外,热锻工艺适用于多种金属材料的加工,包括钢、铝、铜等常见金属,以及不锈钢、钛合金等难加工材料。通过调整加热温度、锻造压力和模具形状等参数,热锻工艺可以生产出形状复杂、尺寸精确的金属制品,满足不同行业的个性化需求。这种灵活性使得热锻工艺在航空航天、汽车制造、机械制造等领域得到了广泛应用。利用高温热锻技术处理木地板底部,有效提升了地板的防潮透气性能,保护地板免受潮湿侵害。
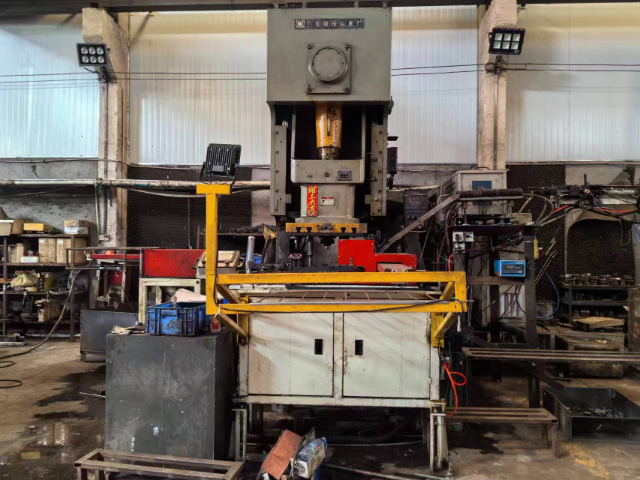
涨紧轮作为传动系统中的重要部件,其质量和性能直接关系到整个系统的稳定性和效率。热锻加工因其能够赋予金属材料优异的力学性能和精确的形状控制能力,成为制造涨紧轮的理想选择。在涨紧轮的热锻加工过程中,金属坯料首先被加热至适宜的温度,使材料内部晶粒软化并具备良好的塑性和延展性。随后,在强大的压力作用下,金属坯料按照预设的模具形状发生塑性变形,形成涨紧轮的复杂轮廓和精细结构。热锻加工不仅确保了涨紧轮的强度高和高韧性,还通过优化材料分布和减少内部缺陷,提高了产品的使用寿命和可靠性。类似热锻中的金属表面处理,木地板的防水层更加牢固,延长了使用寿命。哪里有热锻生产单位
热锻工艺在多层实木地板生产中的应用,增强了层与层之间的结合力,延长了地板的使用寿命。面轮热锻毛坯公司
不锈钢热锻,作为一种先进的金属加工技术,其关键在于利用高温下不锈钢材料的良好塑性和较低的变形抗力,通过压力作用使其发生塑性变形,从而获得所需形状和尺寸的锻件。这一过程通常在高温炉中进行,将不锈钢坯料加热至接近其再结晶温度,此时材料内部原子活动加剧,晶界迁移能力增强,有利于消除加工硬化现象,促进组织均匀化。不锈钢热锻的优势显而易见:首先,它能明显改善材料的力学性能,如提高其强度、硬度和韧性,减少内部缺陷;其次,热锻能够精确控制锻件的尺寸和形状,满足复杂零件的制造需求;再者,由于高温下材料流动性好,易于填充模具,因此热锻件表面光洁度高,后续加工余量小,节约材料成本;热锻过程还能促进不锈钢中合金元素的均匀分布,优化材料组织结构,提高耐腐蚀性和耐磨性。面轮热锻毛坯公司
上一篇: 转子锻件锻造制造厂家
下一篇: 棒套锻打生产加工