316L锻压加工生产厂
锻压工艺的优点在于能够显著提高金属材料的性能。通过锻压,金属材料中的晶粒得到细化,组织更加致密,从而提高了材料的强度和韧性。此外,锻压还能改善金属材料的内部应力状态,减少残余应力,提高材料的疲劳寿命。同时,锻压工艺还能生产出形状复杂、精度高的零件,满足各种复杂工况的需求。随着科技的不断进步,锻压工艺也在不断发展和创新。新型锻造设备和技术的应用,使得锻压工艺更加高效、准确和环保。例如,采用计算机数值模拟技术可以对锻压过程进行精确模拟和优化设计,提高产品的质量和性能。同时,新型环保材料和绿色锻造技术的应用,也减少了锻压过程中的能耗和污染,促进了锻压工艺的可持续发展。精心锻压,尽显金属魅力。316L锻压加工生产厂
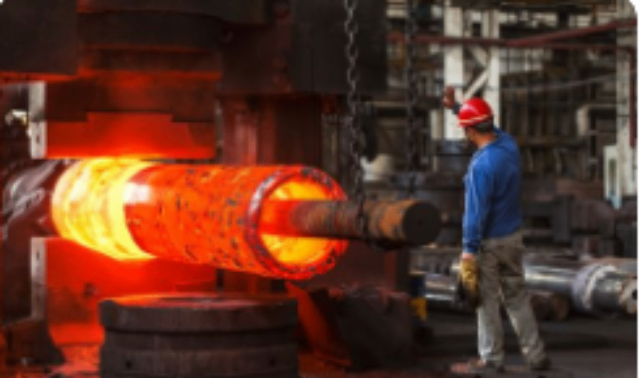
锻压在汽车制造中的工艺特点和优势:提高材料性能:锻压过程中,金属材料受到压力作用产生塑性变形,能够细化晶粒、改善内部组织结构,从而提高材料的强度和韧性。这对于汽车制造中关键部件的制造尤为重要。优化尺寸精度:模锻工艺能够将金属材料置于模具中,通过压力机施加压力使其填充模具型腔,形成精确的零件形状。这种工艺方法能够生产出尺寸精确、表面光洁的零件,满足汽车制造的高精度要求。提高生产效率:锻压工艺可以采用自动化生产线进行大批量生产,生产效率高且质量稳定。这对于汽车制造行业来说具有重要意义,能够降低生产成本并提高市场竞争力。精密锻压锻压技术,塑造金属之魂。
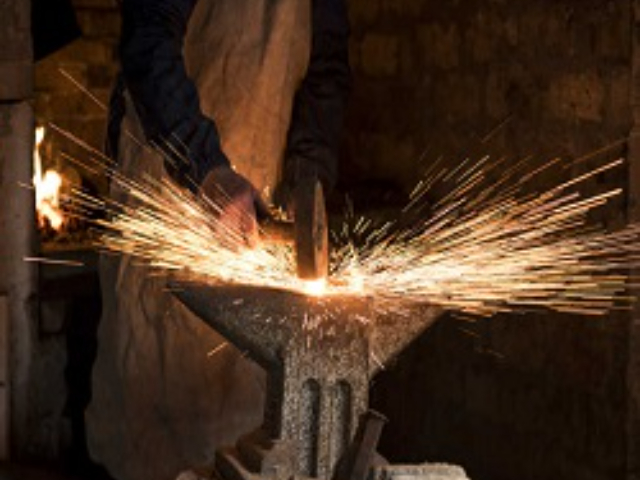
热锻压工艺流程主要包括原料准备、加热、锻造、冷却、清理和检查等步骤。原料准备:选择适当的原材料,包括金属坯料和锻造辅助材料。金属坯料通常为各类金属合金或纯金属,根据需要可以采用不同的规格和形状。锻造辅助材料包括模具、润滑油、冷却水等。加热:将金属坯料放入加热炉中,加热到所需的温度。加热温度和加热时间需要严格控制,避免金属材料过度加热或加热不足。预热温度应控制在金属材料的再结晶温度以上,但不超过其熔点。锻造:加热后的金属坯料放入锻压机或铁锤等设备中进行压制、拉伸、弯曲等变形加工,从而改变其内部组织和物理性质,finally,得到所需形状和尺寸的金属制品。锻造过程需要控制温度、压力和锤击次数等因素,以保证锻件的精度和表面光洁度。 冷却:对锻造后的金属材料进行冷却处理,以使其达到所需的硬度和强度。冷却处理通常采用自然冷却或人工冷却方式,具体选择取决于工件的材质和工艺要求。清理:主要是去除表面氧化皮和其他杂质,以提高工件的表面质量和精度。清理方法包括喷砂、酸洗等。检查:一般锻件要经过外观和硬度检查,重要锻件还要经过化学成分分析、机械性能、残余应力等检验和无损探伤。
然而,直齿轮锻压技术也面临着一些挑战。首先,模具设计和制造难度较大,需要高精度的加工设备和专业的技术人员。其次,锻压过程中的温度和压力控制较为困难,需要经验丰富的操作人员和先进的控制系统。此外,锻压成形还可能产生残余应力和变形等问题,需要通过后续的热处理和校正工艺进行解决。为了克服这些挑战,需要不断研究和改进直齿轮锻压技术,提高模具设计和制造水平,优化工艺参数和控制系统,以降低生产成本和提高产品质量。锻压之力,打造永恒之美。
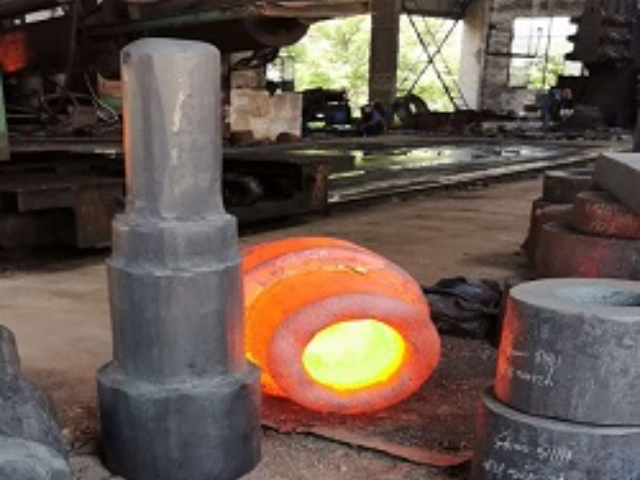
锻压车间主要用途:生产金属锻件:锻压车间主要用于生产各类金属锻件,这些锻件广泛应用于汽车、航空航天、机械制造等多个行业。例如,在汽车制造中,锻压车间生产的锻件可用于发动机零部件、传动系统零件和底盘部件等。热加工与精密锻造:除了基本的锻造加工外,锻压车间还可进行金属的热加工和精密锻造。热加工包括锻造、压铸、挤压等工艺,而精密锻造则能生产出尺寸精度高、形状复杂的金属零件。材料热处理:锻压车间还承担金属材料的热处理工作,通过加热、保温和冷却等工艺过程,改善材料的组织结构和性能。模具制造与产品表面处理:此外,锻压车间还能根据产品需求制造适合的模具,并进行产品的表面处理,以提高产品的外观质量和耐腐蚀性。锻压工艺,是对金属进行深度加工的艺术,赋予其新的生命。传动轴锻压生产加工单位
锻压之下,金属变形而质不变。316L锻压加工生产厂
以某大型锻造企业为例,该企业引进了先进的锻压控制系统,实现了对锻造液压机的自动化控制和管理。该系统具有以下特点:采用了高性能的控制器和传感器,实现了对锻造液压机压力、位移、速度等参数的精确控制。配备了触摸屏操作界面和人机交互系统,使操作人员能够方便地设定控制参数和监控设备运行状态。实现了与操作机的联动控制,提高了生产效率和产品质量。采用了模糊控制与PID控制相结合的控制策略,有效克服了传统PID控制的缺陷,提高了系统的稳定性和可靠性。通过引入锻压控制系统,该企业实现了对锻造液压机的精确控制和自动化管理,很大提高了生产效率和产品质量。同时,系统的安全性和可维护性也得到了有效保障。316L锻压加工生产厂