齿轮锻压生产加工
锻压在汽车制造中的工艺特点和优势:提高材料性能:锻压过程中,金属材料受到压力作用产生塑性变形,能够细化晶粒、改善内部组织结构,从而提高材料的强度和韧性。这对于汽车制造中关键部件的制造尤为重要。优化尺寸精度:模锻工艺能够将金属材料置于模具中,通过压力机施加压力使其填充模具型腔,形成精确的零件形状。这种工艺方法能够生产出尺寸精确、表面光洁的零件,满足汽车制造的高精度要求。提高生产效率:锻压工艺可以采用自动化生产线进行大批量生产,生产效率高且质量稳定。这对于汽车制造行业来说具有重要意义,能够降低生产成本并提高市场竞争力。锻压转子,为高效运行提供有力保障。齿轮锻压生产加工
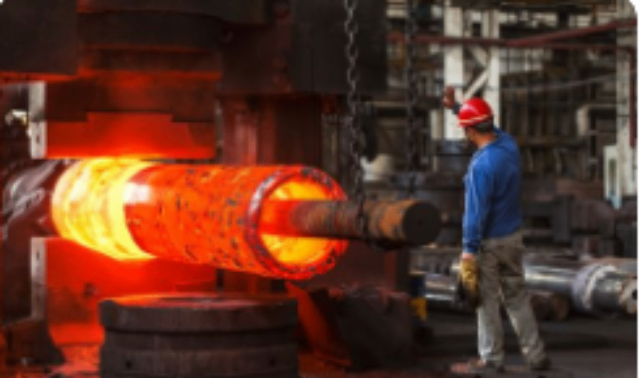
热锻压工艺特点:改善金属塑性:提高温度能明显改善金属的塑性,使金属材料在锻压过程中更容易变形,从而提高工件的内在质量,减少开裂现象的发生。减小变形抗力:高温条件下,金属的变形抗力减小,使得锻压过程更加容易进行,降低了所需锻压机械的吨位,提高了生产效率。提高工件质量:高温变形有利于提高工件的内在质量,如强度、硬度、韧性等物理性能。同时,热锻压还能消除金属材料的内部应力,提高工件的尺寸精度和表面光洁度。适用范围广:热锻压适用于加工各种金属材料,特别是加工工件大、厚,材料强度高、塑性低的金属材料时,热锻压具有明显优势。托轮锻压生产厂家高温下的锻压,是对金属的真正考验,塑造出坚不可摧的精品。
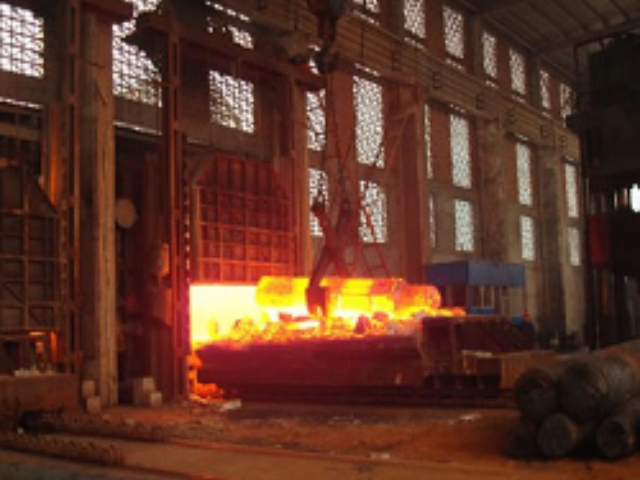
锻压的智能化发展是制造业技术革新的重要方向之一。随着人工智能、物联网、大数据等技术的快速发展,锻压设备正逐步实现智能化转型。智能化锻压设备通过集成先进的传感器、控制系统和数据分析软件,能够实时监控生产过程中的各项参数,如温度、压力、速度等,从而确保锻压产品的质量和稳定性。同时,智能化技术还能优化生产流程,提高生产效率,降低生产成本。在锻压智能化发展的过程中,数字化技术的应用尤为关键。数字化技术可以将锻压设备的运行状态、生产数据等信息进行实时采集和传输,为生产决策提供数据支持。此外,数字化技术还能实现远程监控和故障诊断,提高设备的维护效率和可靠性。未来,锻压的智能化发展将更加注重个性化定制和柔性化生产。通过智能化技术,企业可以根据市场需求和客户需求快速调整生产计划和产品规格,实现快速响应和定制化生产。同时,智能化技术还能提高生产的灵活性和适应性,满足不同行业和不同客户的需求。
锻压的时间,在金属加工领域中,特指某些特定工艺过程中的时间段。以点焊为例,锻压时间通常指的是从焊接电流结束到撤消电极压力之间的一段时间。这段时间对于焊接接头的形成和性能具有重要影响。在锻压加工过程中,时间的控制是至关重要的。它直接影响到材料的变形程度、组织的细化以及最终产品的性能。如果锻压时间过短,材料可能无法充分变形,导致内部组织不均匀,影响产品的力学性能和可靠性。相反,如果锻压时间过长,可能会导致材料过热、晶粒粗化,甚至产生裂纹等缺陷。因此,在锻压加工中,需要根据具体的材料、工艺和设备条件来合理确定锻压时间。这通常需要通过实验和经验积累来不断优化和调整。同时,还需要注意控制锻压过程中的温度、压力等参数,以确保锻压过程的稳定性和产品的质量。锻压转子,提高机械传动效率。
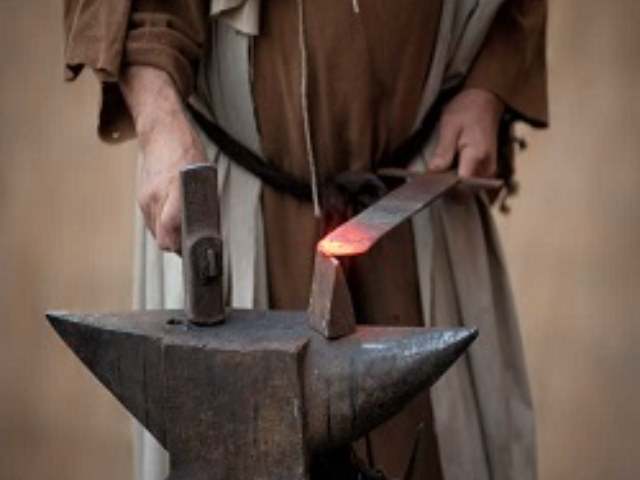
转子锻压技术也在不断向高精度、高效率和高自动化的方向发展。高精度锻压技术通过采用先进的数控系统和精密的模具设计,实现了对转子尺寸的精确控制,提高了转子的性能稳定性和可靠性。高效率锻压技术则通过优化工艺参数和采用先进的锻压设备,大幅提高了转子的生产效率和产量。例如,采用热模锻技术可以实现对金属坯料的连续加热和锻压,提高了生产效率;采用多工位锻压设备则可以同时加工多个转子,进一步提高了生产效率。高自动化锻压技术则通过引入机器人、自动化控制系统等先进技术,实现了对转子锻压过程的各方面自动化控制。这不仅提高了生产效率,还降低了劳动强度,减少了人为因素对产品质量的影响。例如,采用机器人进行坯料的取放和装夹可以实现对坯料的精确定位和快速更换;采用自动化控制系统则可以对锻压过程中的温度、压力等参数进行实时监控和调整,确保产品质量的稳定性。每一块锻压出的金属,都是匠人辛勤劳动的结晶。锻压制造厂电话
锻压工艺,彰显非凡实力。齿轮锻压生产加工
锻压控制系统是现代金属加工行业中不可或缺的一部分,它对于提高生产效率、保证产品质量以及实现生产自动化具有至关重要的作用。锻压控制系统是指对锻压设备进行操作、监控和管理的系统,它通过对锻压设备的运动轨迹、速度、力度等参数进行精确控制,实现对金属材料的塑性变形加工。锻压控制系统通常由硬件和软件两部分组成,硬件部分包括控制器、传感器、执行机构等,软件部分则包括控制算法、操作界面等。未来随着技术的不断发展和创新,锻压控制系统将在更多领域得到应用和发展。齿轮锻压生产加工
上一篇: 齿轮坯红冲生产加工厂
下一篇: 321红冲毛坯厂