偏心轴热模锻加工工厂
随着科技的不断进步和工业的快速发展,热模锻技术也在不断创新和完善。未来,热模锻技术将更加注重精密化、高效化和智能化的发展。例如,通过采用先进的加热和冷却技术,可以进一步提高锻件的精度和性能;通过引入自动化和智能化设备,可以实现热模锻过程的全自动化和智能化控制,提高生产效率和产品质量。同时,热模锻技术在新能源汽车、航空航天等高级制造领域的应用也将不断拓展。例如,在新能源汽车领域,热模锻技术可以用于制造高性能的电动机壳体和传动系统零部件;在航空航天领域,热模锻技术则可以用于制造强度高的飞机起落架和发动机部件。这些应用将进一步推动热模锻技术的发展和创新,为工业制造领域带来更多的机遇和挑战。热模锻后的锻件通常需要进行热处理,以进一步改善其机械性能和稳定组织。偏心轴热模锻加工工厂

在医疗器械领域,不锈钢热模锻件同样具有重要地位。不锈钢锻造的手术器械、植入物等产品因其良好的生物相容性和耐腐蚀性而备受青睐。例如,人工关节、心脏支架等医疗器械通常采用不锈钢锻造制造。这些产品需要直接与人体组织接触,不锈钢锻造件以其无毒、无害、耐腐蚀等特性,确保了医疗器械的安全性和有效性。不锈钢热模锻技术之所以能够在多个领域得到广泛应用,主要得益于其独特的技术特点和优势。首先,不锈钢热模锻件具有优异的力学性能和耐腐蚀性,能够满足各种复杂工作环境的需求;其次,不锈钢热模锻技术能够实现高精度、高效率的加工,降低生产成本并提高产品质量;不锈钢热模锻件还具有良好的可塑性和可加工性,便于后续加工和组装。铝热模锻制造供应商热模锻过程中的温度监控是保证锻件质量的重要手段之一。
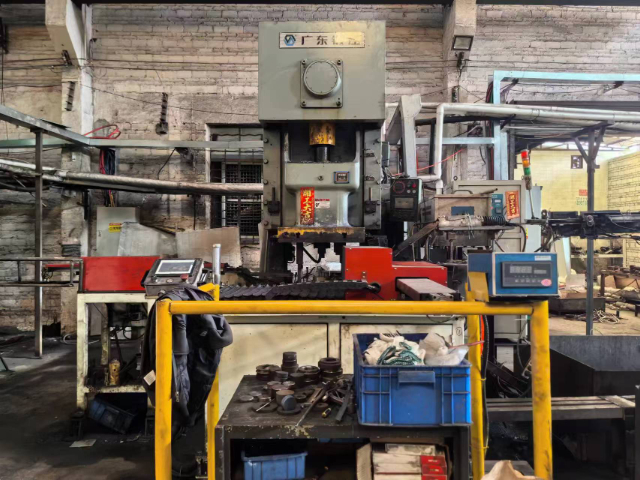
不锈钢热模锻技术的工艺流程主要包括以下几个步骤:材料准备:选择合适的不锈钢材料,并进行化学成分、力学性能等指标的检验,确保材料质量符合要求。毛坯加热:将不锈钢毛坯放入加热炉中,加热至预定的温度(通常为材料的奥氏体化温度以上),并保持一定时间,使毛坯内部温度均匀,同时减少加热过程中的氧化和脱碳现象。模具预热:为了提高模具的使用寿命和锻件的表面质量,通常需要将模具预热至一定温度(如150~200℃,有时可预热到300℃),以减少模具与毛坯之间的温差应力。模锻成形:将加热后的毛坯放入预热好的模具中,施加足够的压力使毛坯发生塑性变形,填充模具型腔,形成所需的锻件形状。此过程中需要严格控制锻造温度、变形速率和变形量等参数,以确保锻件的质量。切边与修整:锻造成形后,通常需要对锻件进行切边处理,去除多余的飞边和毛刺。随后进行表面修整和尺寸检验,确保锻件符合设计要求。热处理与检验:根据锻件的用途和要求,可能需要进行后续的热处理(如淬火、回火等)以改善其力学性能。
热模锻是一种重要的金属加工工艺,它利用高温下的金属塑性,通过模具对金属进行塑形,以获得所需形状和尺寸的锻件。这一工艺过程中,金属在加热后变得柔软且易于塑形,模具则起到引导和限定金属流动的作用,确保锻件形状的精确性和一致性。热模锻广泛应用于汽车、航空、机械等多个领域,是制造高质量、高性能零部件的关键技术之一。通过热模锻,可以实现材料的优化利用,提高产品的力学性能和耐用性,同时降低生产成本,提升生产效率。针对不同行业的需求,热模锻工艺可以灵活调整以满足特定的生产要求。
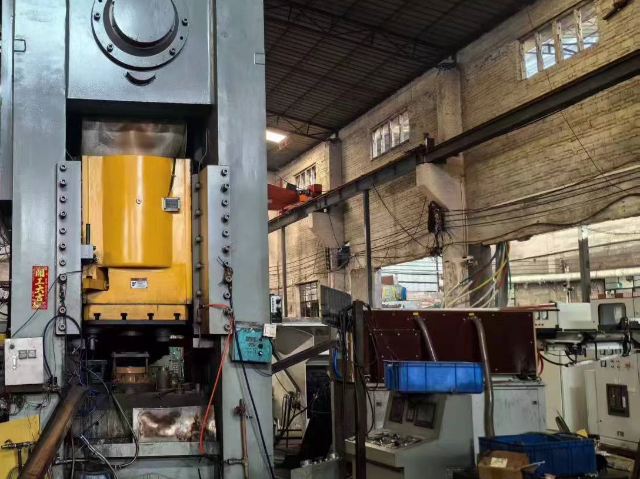
热模锻工艺的优势与挑战优势提高材料利用率:热模锻工艺能够充分利用材料的塑性变形能力,减少材料的浪费。改善锻件性能:通过加热和高压成形,可以明显改善锻件的机械性能和表面质量。降低生产成本:热模锻工艺能够实现大规模生产,降低单个锻件的生产成本。挑战模具成本高:高精度模具的设计和制造需要投入大量资金和时间。工艺控制难度大:成形过程中的温度、压力和速度等参数需要严格控制,否则可能影响锻件的质量。材料选择受限:并非所有金属材料都适合进行热模锻加工,需要根据材料的特性进行选择。通过对热模锻过程中金属微观组织的观察和分析,可以深入了解其变形机制。链轮热模锻制造单位
热模锻是一种利用高温下金属材料的良好塑性和流动性进行锻造的工艺方法。偏心轴热模锻加工工厂
热模锻,又称热锻,是在金属再结晶温度以上进行的锻造工艺。在此过程中,金属材料的塑性显著提高,变形抗力降低,使得复杂的形状和精确的尺寸得以实现。涨紧轮作为机械传动系统中的关键部件,其制造质量直接影响整个系统的运行稳定性和使用寿命。因此,采用热模锻工艺生产涨紧轮,能够确保产品具有强度高、高耐磨性和良好的尺寸精度。在实际生产中,涨紧轮热模锻工艺已被广泛应用于多个领域。例如,在汽车制造行业中,发动机和传动系统中的涨紧轮多采用热模锻工艺生产。这些涨紧轮不仅具有优异的力学性能和耐磨性,还能确保发动机和传动系统的正常运行。此外,在工程机械、航空航天等领域中,涨紧轮热模锻工艺也得到了广泛应用。偏心轴热模锻加工工厂
上一篇: 齿轮热锻加工生产有限公司
下一篇: 锻造锻件生产有限公司报价