铁热锻加工生产单位
涨紧轮热煅完成后,还需进行一系列的热处理和检验工作以确保产品质量。热处理包括退火、正火、淬火和回火等工序,旨在进一步调整材料的组织结构和性能,消除锻造过程中产生的残余应力和脆性相。检验工作则包括尺寸精度检测、表面质量检查、力学性能测试和疲劳寿命试验等,以多面评估涨紧轮的性能指标是否达到设计要求。对于不合格的产品,需进行返工或报废处理,以确保出厂的涨紧轮均能满足客户的使用需求。涨紧轮热煅工艺是一项复杂而精细的制造技术,涉及温度控制、模具材料选择、工艺参数优化以及热处理与检验等多个环节。通过科学合理的热煅工艺控制,可以生产出高质量、高性能的涨紧轮产品,为机械设备的稳定运行提供有力保障。类似热锻中的热处理工艺,有效去除了木地板中的有害物质,提升了居住健康性。铁热锻加工生产单位
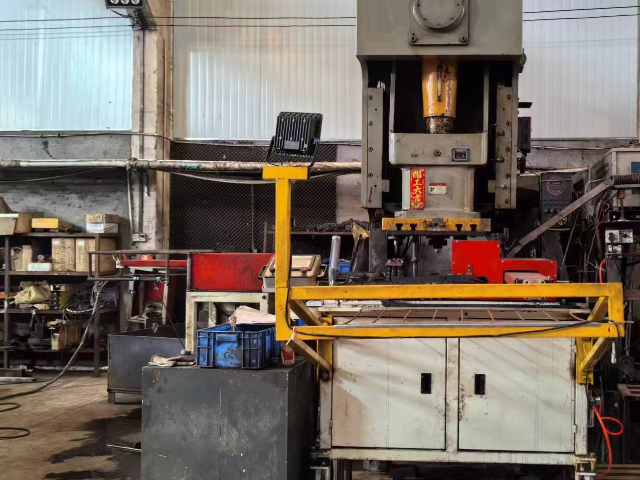
随着科技的进步和环保意识的增强,合金钢热锻工艺也在不断创新与升级,以适应更加复杂多变的工业需求和日益严格的环保标准。一方面,智能化、自动化技术的应用,使得热锻生产线更加高效、精细、灵活。通过引入先进的控制系统和传感器技术,可以实现对加热温度、锻造压力、变形速度等关键参数的实时监测与调整,确保产品质量的一致性和稳定性。同时,机器人、自动化搬运系统等设备的应用,也很大减轻了工人的劳动强度,提高了生产效率和安全性。铝热锻制造工厂类似热锻的形变控制技术,帮助木地板在加工过程中保持精细的尺寸规格。
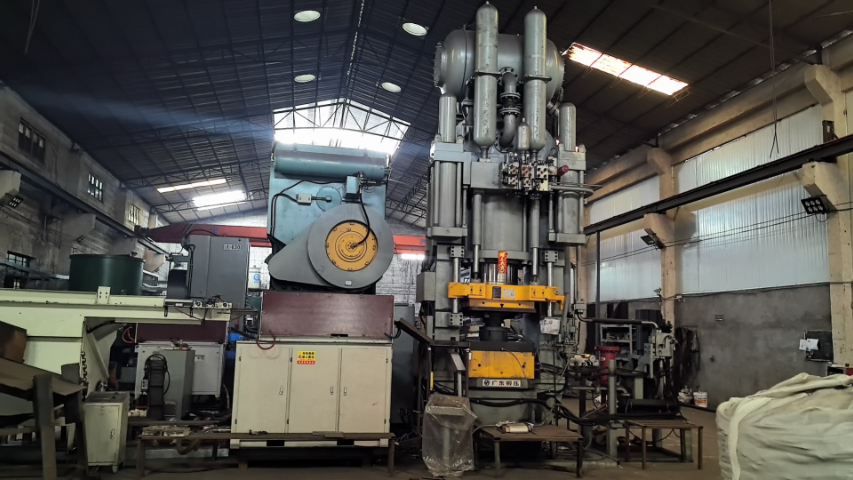
在汽车制造业中,热锻加工技术被广泛应用于发动机零部件的生产。例如,曲轴、连杆等关键部件,由于其形状复杂、受力要求高,采用热锻加工可以确保部件的强度和韧性达到设计要求。同时,热锻加工还能有效减少部件的重量,提高燃油经济性。在航空航天领域,热锻加工技术更是不可或缺。航空发动机叶片、涡轮盘等高温高压部件,其材料多为难加工的镍基合金或钛合金,通过热锻加工可以实现复杂形状的精确成形,同时保证部件在高温环境下的稳定性和耐久性。
热锻工艺的实现离不开先进的设备和技术支持。热炉、锻压机、冷却系统等设备是热锻生产线上的关键组成部分。热炉负责将金属坯料加热至适宜温度,锻压机则通过施加压力使金属材料发生塑性变形。冷却系统则用于控制加热后的金属坯料的温度,避免其过度变形或热裂。随着科技的发展,热锻设备不断升级换代,自动化程度不断提高。现代热锻生产线集成了计算机控制、机器人操作等先进技术,实现了从原料准备到成品出库的全程自动化生产。这不仅提高了生产效率和质量稳定性,还降低了劳动强度和人为因素导致的生产风险。类似热锻中的压力施加,木地板在压制成型阶段采用高压处理,确保结构紧密,不易起翘。
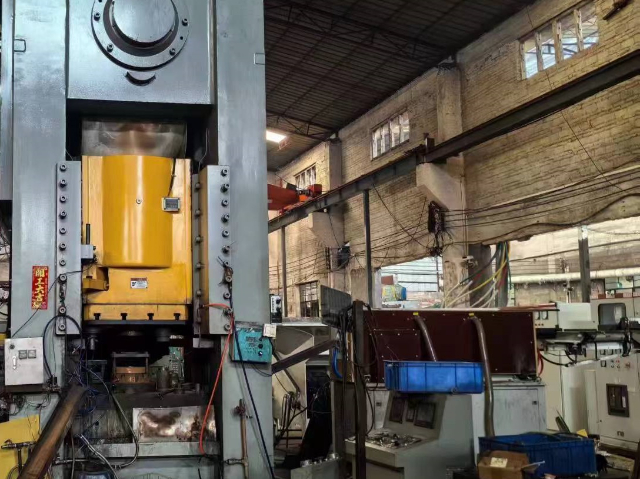
在热锻加工过程中,温度控制是关键环节之一,直接关系到锻件的成型质量、组织性能及后续加工性能。原材料需根据材料特性和锻造工艺要求,在加热炉中加热至适当的温度范围。过高的温度会导致材料晶粒粗大、氧化严重,甚至出现过烧现象;而过低的温度则会影响材料的塑性和变形抗力,增加锻造难度。因此,精确控制加热温度至关重要。同时,还需注意加热的均匀性,确保材料内外温度一致,避免出现局部过热或过冷导致的应力集中和裂纹等问题。为实现这一目标,可采用多段加热、保温时间控制、炉内气流循环等措施,以提高加热效率和均匀性。借鉴热锻工艺,木地板边缘进行了特殊热处理,增强了耐磨边效果。钢铁热锻单位
热锻工艺处理的木地板表面,易于清洁保养,长期保持光洁如新。铁热锻加工生产单位
随着科技的进步和市场需求的变化,铝合金热锻技术也在不断创新与发展。一方面,新材料、新工艺的引入为铝合金热锻注入了新的活力。如高性能铝合金的研发与应用,使得热锻件在强度、韧性、耐腐蚀性等方面有了明显提升;而数值模拟技术(如有限元分析)的应用,则使得锻造过程的预测和优化成为可能,很大缩短了产品开发周期,降低了研发成本。另一方面,智能化、自动化水平的提升也推动了铝合金热锻生产的转型升级。通过引入智能控制系统、机器人辅助操作、在线检测与监控等技术手段,实现了生产过程的精细控制和数据化管理,提高了生产效率和产品质量稳定性。未来,随着绿色制造理念的深入人心,铝合金热锻技术还将更加注重节能减排和资源循环利用,推动行业向更加环保、高效、可持续的方向发展。同时,跨学科融合也将成为铝合金热锻技术创新的重要方向,如材料科学、机械工程、信息技术等领域的深度融合,将为铝合金热锻技术的突破提供新的思路和动力。铁热锻加工生产单位
上一篇: 辊锻件锻造加工生产供应商
下一篇: 链轮模锻生产厂