固定座热模锻加工厂
热模锻作为一种重要的金属加工工艺,具有多个明显特点。首先,热模锻能够实现高精度和复杂形状的制造。在高温下,金属具有较好的塑性和流动性,能够通过模具的引导填充到模具的每个角落,形成精确且复杂的形状。这一特点使得热模锻在制造高精度零部件方面具有独特优势。其次,热模锻能够改善金属的力学性能。在高温和压力的作用下,金属内部的晶粒结构会发生优化,从而提高锻件的强度和韧性。这种力学性能的改善使得热模锻件在承受高负荷和冲击时具有更好的耐用性。此外,热模锻还具有高效、节能的特点。相比其他金属加工工艺,热模锻能够实现一次成型,减少后续加工步骤,提高生产效率。同时,热模锻过程中的能量利用也更加充分,有助于降低生产成本。综上所述,热模锻以其高精度、改善金属力学性能、高效节能等特点,在金属加工领域发挥着重要作用,为各行业的制造提供了有力支持。先进的检测设备和技术手段为热模锻件的质量控制提供了有力保障。固定座热模锻加工厂
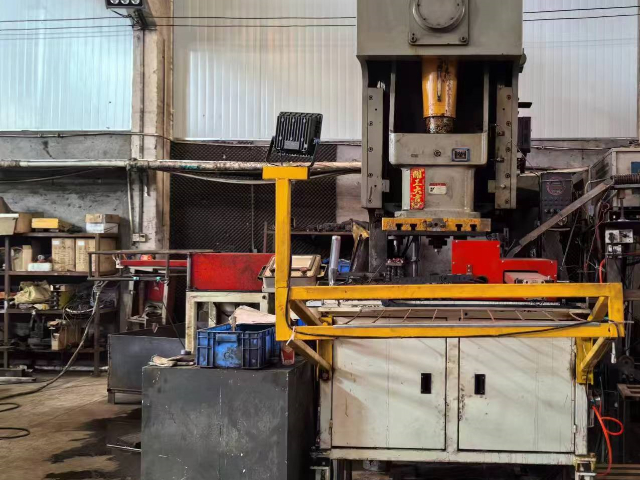
材料准备是热模锻工艺的第一步,也是基础。在这一阶段,需要选择适合锻造要求的金属材料,如钢、铝、铜等。这些材料应具有良好的塑性和可锻性,以满足后续加工的需求。同时,还需要对原材料进行初步处理,如切割成适当长度的坯料,并进行表面清理,以去除油污、锈蚀等杂质。加热处理是热模锻工艺中的关键环节。将准备好的金属材料放入加热炉中,加热至一定温度(通常在1000℃以上),使其达到足够的塑性和流动性。加热温度和时间需要根据材料的种类、厚度以及所需的成形性能进行调整。过高的温度可能导致材料过烧,而过低的温度则可能使材料难以成形。环形热模锻生产加工有限公司为了提高热模锻的生产效率,现代工厂常采用自动化加热炉和机械手进行上下料操作。
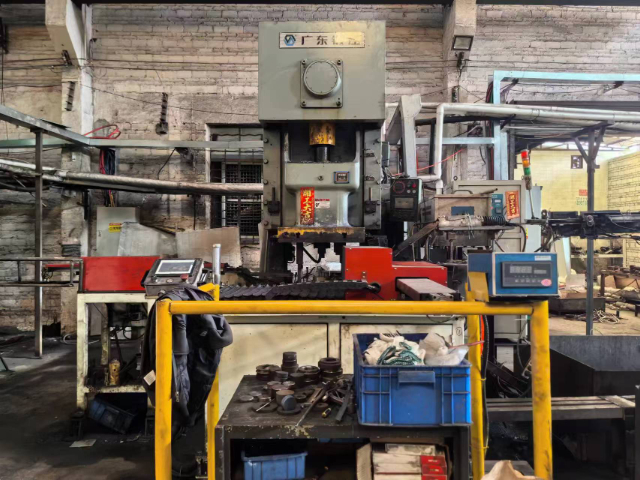
热模锻是一种重要的金属加工工艺,它利用高温下的金属塑性,通过模具对金属进行塑形,以获得所需形状和尺寸的锻件。这一工艺过程中,金属在加热后变得柔软且易于塑形,模具则起到引导和限定金属流动的作用,确保锻件形状的精确性和一致性。热模锻广泛应用于汽车、航空、机械等多个领域,是制造高质量、高性能零部件的关键技术之一。通过热模锻,可以实现材料的优化利用,提高产品的力学性能和耐用性,同时降低生产成本,提升生产效率。
不锈钢热模锻技术的工艺流程主要包括以下几个步骤:材料准备:选择合适的不锈钢材料,并进行化学成分、力学性能等指标的检验,确保材料质量符合要求。毛坯加热:将不锈钢毛坯放入加热炉中,加热至预定的温度(通常为材料的奥氏体化温度以上),并保持一定时间,使毛坯内部温度均匀,同时减少加热过程中的氧化和脱碳现象。模具预热:为了提高模具的使用寿命和锻件的表面质量,通常需要将模具预热至一定温度(如150~200℃,有时可预热到300℃),以减少模具与毛坯之间的温差应力。模锻成形:将加热后的毛坯放入预热好的模具中,施加足够的压力使毛坯发生塑性变形,填充模具型腔,形成所需的锻件形状。此过程中需要严格控制锻造温度、变形速率和变形量等参数,以确保锻件的质量。切边与修整:锻造成形后,通常需要对锻件进行切边处理,去除多余的飞边和毛刺。随后进行表面修整和尺寸检验,确保锻件符合设计要求。热处理与检验:根据锻件的用途和要求,可能需要进行后续的热处理(如淬火、回火等)以改善其力学性能。 在热模锻生产中,采用感应加热可以快速且均匀地加热金属材料。
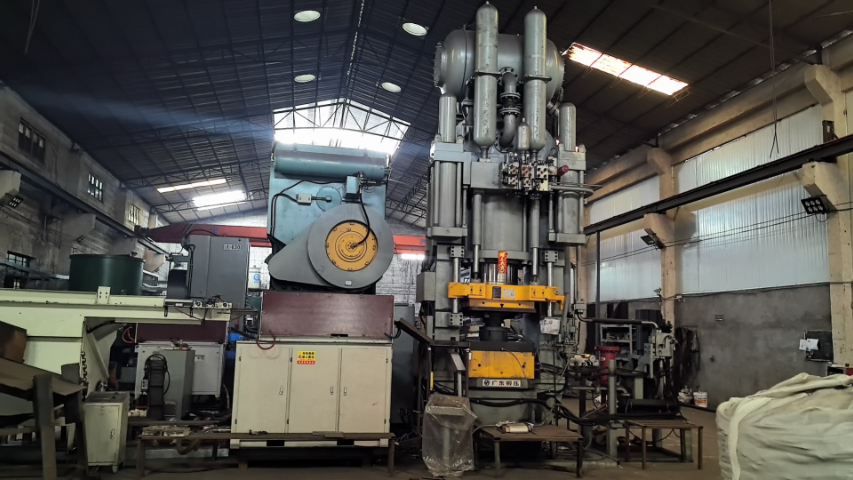
在航空航天领域,转子热模锻技术更是发挥着不可替代的作用。航空航天器对零部件的性能要求极高,必须能够承受极端的环境条件和复杂的力学载荷。发动机部件:航空发动机中的转子部件,如风扇叶片、压气机叶片和涡轮叶片等,是发动机性能的关键。这些部件不仅要求具有强度高和高温性能,还需要具有精确的尺寸和形状。转子热模锻技术能够确保这些部件的精确成形和内部组织的优化,提高发动机的推力和效率。结构部件:航空航天器的机身、机翼等结构部件也常采用转子热模锻技术制造。这些部件需要具有强度高、高刚性和轻量化的特点。转子热模锻技术能够满足这些要求,为航空航天器提供坚固而轻盈的结构支撑。热模锻工艺中的温度梯度控制对于减少锻件内应力和提高组织均匀性至关重要。热模锻毛坯公司价格
通过对热模锻过程中金属微观组织的观察和分析,可以深入了解其变形机制。固定座热模锻加工厂
不锈钢热模锻作为一种重要的金属加工技术,在多个领域具有广泛的应用场景。在航空航天领域,不锈钢热模锻技术发挥着至关重要的作用。由于航空航天设备对零件的强度、重量和可靠性要求极高,不锈钢锻造件能够满足这些苛刻的要求。具体而言,不锈钢热模锻件常用于制造发动机部件(如涡轮叶片)、起落架零件以及结构件等。这些部件需要承受高温、高压和复杂的工作环境,不锈钢锻造件以其优异的力学性能和耐腐蚀性,确保了航空航天设备的安全性和可靠性。固定座热模锻加工厂