东莞生产进度可视化管理公司
选择前端框架:选择适合的前端框架(如React、Vue、Angular等)来开发可视化界面;设计UI/UX:设计用户友好的界面和交互方式,确保用户能够轻松理解和使用系统;实现图表和组件:使用前端框架和可视化库(如ECharts、D等)实现各种图表和组件,以展示数据和指标;实现实时更新:通过轮询、WebSocket等技术实现数据的实时更新和展示;定期对可视化系统进行维护和升级,确保系统的稳定性和安全性;根据生产现场的实际需求,不断优化系统功能和界面设计;收集用户反馈和建议,持续改进ESOP系统的性能和用户体验;利用ESOP系统收集的生产数据,进行深入的分析和挖掘;找出生产过程中的瓶颈和浪费环节,提出优化建议并付诸实施;监控生产过程的实时数据,确保生产按照计划进行,并及时发现和解决问题。检测工位使用QC功能,发现不良品时,根据不良原因进行扫码,即可自动录入质检数据,并同步至看板。东莞生产进度可视化管理公司
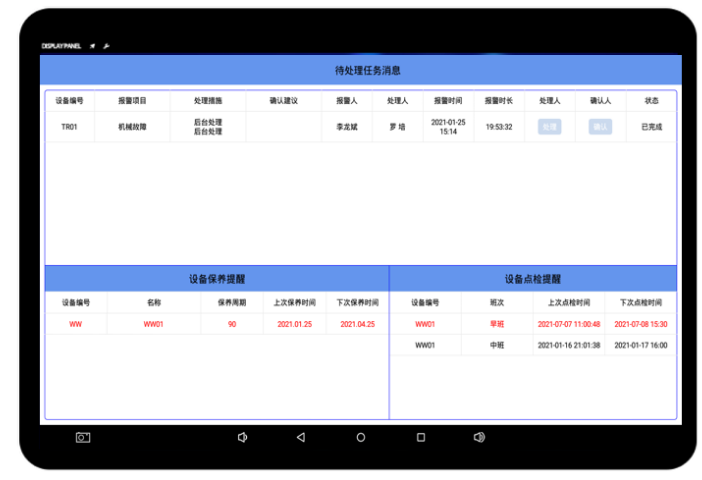
实时数据获取:生产看板通过连接车间内的各种传感器、设备和其他数据源,实时采集生产过程中的关键数据。这些数据可能包括设备运行状态、生产进度、产品质量检测结果等;利用PDA(个人数字助理)或其他移动设备进行扫码操作,可以快速准确地获取生产工序中的物料信息、产品信息、数量等实时数据;实时数据获取确保了生产看板上的信息,有助于管理人员及时了解生产现场的情况;生产看板能够将来自不同数据源的数据进行整合,并以直观、易懂的方式展示给管理人员。这包括使用图表、图形、数字等多种形式来展示生产数据。宁波精益制造可视化管理介绍展示实时数据、质检数据等相关信息。
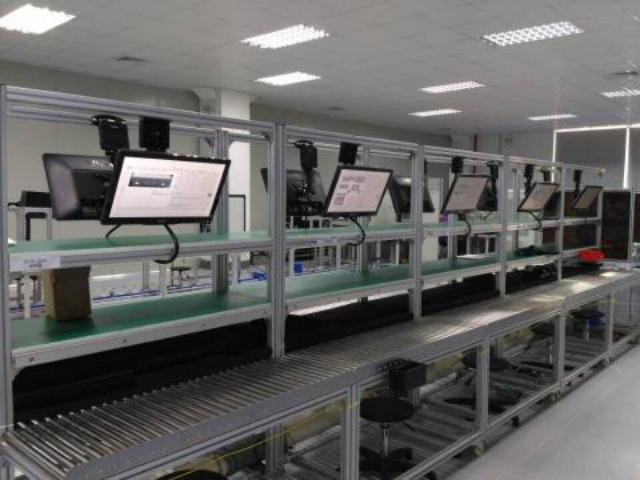
系统根据预设的质量检测标准,对采集到的数据进行自动分析和判断;一旦发现质量数据超出标准范围或存在异常情况,系统会立即触发预警机制,通知相关人员进行处理;可视化系统提供直观的质量数据可视化界面,将实时质量数据以图表、报表等形式展示给用户;用户可以方便地查看生产过程中的质量趋势、合格率、不良品率等关键指标,及时发现潜在问题。系统对采集到的质量数据进行统计分析,找出生产过程中的质量问题及其原因;基于分析结果,系统可以提出改进建议,如优化工艺参数、调整设备状态、改进检测方法等;这些改进建议可以指导企业持续改进生产过程,提高产品质量和客户满意度。
安灯呼叫流程:安灯呼叫流程:呼叫——接任务——完成任务——呼叫人确认完成——系统自动计算完成任务时间;在一体机可查询呼叫记录,包括报警人、处理人、报警时长、状态等。叫料:在ESOP侧边栏展示当前工单的BOM信息,缺料时点击呼叫,被呼叫人能快速得知缺乏的是哪种物料,提高工作效率;BOM信息设置方式:一是在设置SOP模板时由人工输入BOM信息;二是对接甲方ERP系统,抓取BOM信息;系统可以与VGA物流车互联,需VGA物流车提供通讯接口。可视化管理是一种以图表和图形形式展示数据和信息的管理方法。
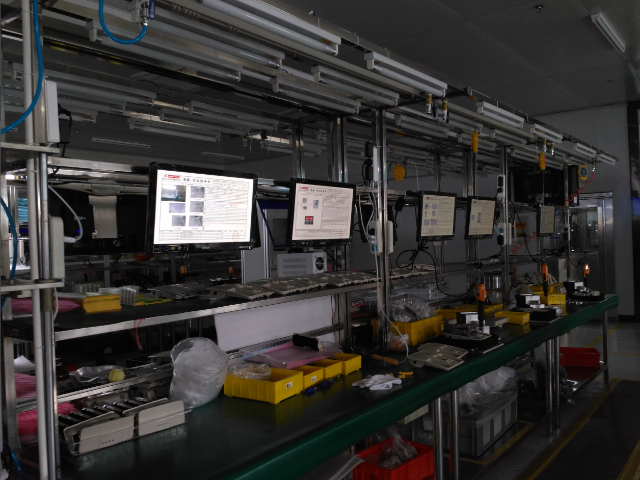
车间管理中的培训与教育可视化:利用ESOP可视化资源对新员工进行培训,帮助他们更快地掌握设备操作和维护技能;定期组织员工观看操作视频、安全警示片等可视化教育资源,提高员工的安全意识和操作技能;持续改进可视化:通过可视化手段展示车间管理的持续改进成果,如生产效率提升、质量改进、成本降低等;鼓励员工提出改进建议,并将建议通过可视化方式展示出来,激发员工的创新精神和参与热情。通过实施可视化管理,车间管理者可以更加高效地管理车间资源,提高生产效率和质量,降低生产成本和安全事故发生率,为企业创造更大的价值。通过扫描或定时方式进行文件的实时发布。杭州设备可视化管理工具
可将作业指导文件转化为电子文档。东莞生产进度可视化管理公司
改进目标的管理包括生产效率管理、担负任务的管理、目标实现率的管理、降低库存管理和降低不合格品的管理等;进度管理包括交货期管理、进度管理、达标管理、定购管理和设备运行管理等;日程管理包括个人出勤管理、个人出差管理和岗位管理等;技能管理包括生产员工的多能化管理、技术人员的多能化管理、管理人员的多能化管理和岗位定期轮换管理等;建立设备维护的可视化管理系统,包括维护计划、维护记录以及维护预警等功能;通过系统提示,管理人员可以及时了解设备的维护状态,避免设备因未及时维护而出现故障;使用可视化工具展示设备的维护历史数据,帮助管理人员分析设备的故障模式和故障趋势,以便制定更有效的维护策略。东莞生产进度可视化管理公司
深圳市昇航软件科技有限公司汇集了大量的优秀人才,集企业奇思,创经济奇迹,一群有梦想有朝气的团队不断在前进的道路上开创新天地,绘画新蓝图,在广东省等地区的商务服务中始终保持良好的信誉,信奉着“争取每一个客户不容易,失去每一个用户很简单”的理念,市场是企业的方向,质量是企业的生命,在公司有效方针的领导下,全体上下,团结一致,共同进退,**协力把各方面工作做得更好,努力开创工作的新局面,公司的新高度,未来深圳市昇航软件科技供应和您一起奔向更美好的未来,即使现在有一点小小的成绩,也不足以骄傲,过去的种种都已成为昨日我们只有总结经验,才能继续上路,让我们一起点燃新的希望,放飞新的梦想!
上一篇: 江门SOP电子作业可视化管理品牌
下一篇: 惠州生产看板可视化管理系统