江苏机床床身铸件厂商
机床床身的稳定性受环境因素影响较大,尤其是震动和湿度。应确保机床安装在坚实的地基上,尽量远离大型振动源;必要时可采取减震措施,如加装减震垫等。另外,对于湿度较高的环境,应注意做好机床床身的防潮处理,防止水分侵蚀金属材料,造成生锈、变形等问题。根据机床的实际使用情况和制造商的推荐,定期进行机床的大修与精度校验。通过调整、修复、更换磨损部件等方式,恢复机床原有的几何精度和技术性能。在此过程中,机床床身的检查与修复尤其重要,任何微小的变形或磨损都可能严重影响整体的加工精度。机床床身实型铸造生产中采用聚苯乙烯泡塑模样应用呋哺树脂自硬砂造型。江苏机床床身铸件厂商
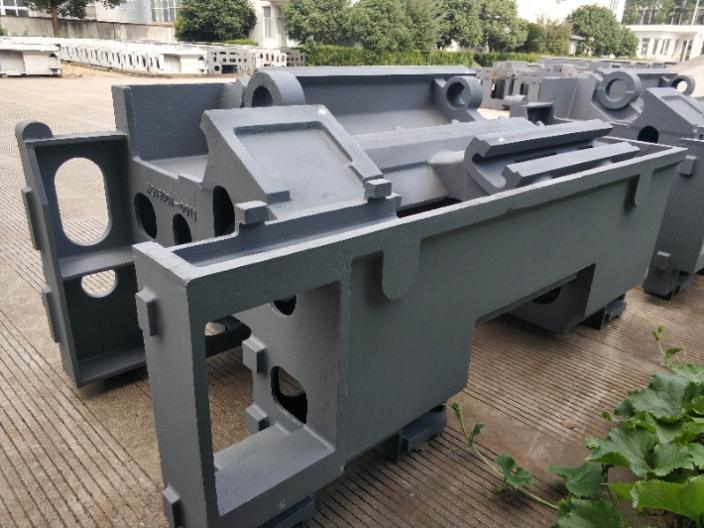
大型机床床身铸件的退火处理:铸件需经过两次人工时效处理,去除内应力。从而使铸件内部结构稳定,不易变形。大规格的机床床身铸件可拼接制作,铸件时可分开来铸。加工时进行整体加工,使其安装及使用精度。机床床身用铸件还是焊接好?这要从床身的稳定性、工艺性和成本等问题分析。不论是铸造的还是焊接的,都存在着热加工过程。既然如此,冷却后在结构内部必然存在着残余应力。残余应力能够使得机床几何形状处于不稳定状态,这对于机床这个加工母机来讲显然是不允许的。工艺上,对于铸造机床体常在铸造后给予时效处理;焊接床身则给予消应力退火处理,以消除这些残余应力的威胁,然后再进行加工成为床身产品。上海超精密机床床身铸件销售费用机床床身铸件需要进行磨削加工达到一定的表面光洁度才可投入使用。
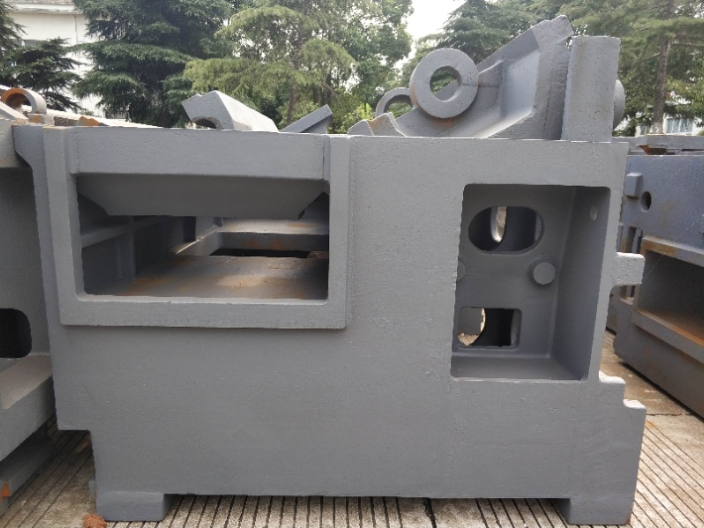
机床床身的使用寿命与其制造材料密切相关。良好的铸铁是目前主流的床身制造材料,因其具有良好的耐磨性、抗压强度和减震性能。高牌号的灰铸铁或球墨铸铁被普遍应用,它们内部结构紧密,能有效抵抗长时间重载荷下的变形和疲劳裂纹,从而明显延长床身寿命。此外,如果采用更先进的合金铸铁或者经过热处理强化的材料,床身的使用寿命还将进一步提升。机床床身的设计与制造工艺也是决定其使用寿命的关键因素。合理的设计能够有效分散受力,避免局部应力集中导致的疲劳失效;精密的加工和装配工艺可以确保床身导轨面的平面度和平行度,减少磨损并保持长期稳定的精度。同时,合理的润滑系统设计和实施,能够降低各运动副之间的摩擦损耗,从而延长床身的使用寿命。
机床床身的表面处理方式——材料选择与铸造后处理:在材料层面,机床床身通常选用良好灰口铸铁如HT200至HT300系列,这种材料具有良好的耐磨性、减震性和切削加工性,并且铸件内部组织均匀,抗拉及抗弯强度高。在铸造成型后,床身会经过一系列热处理工序,包括退火和表面淬火。退火可以消除铸件内部的残余应力,改善其机械性能,提高材料韧性;而表面淬火则主要增强床身表面硬度,减少因长时间受力或摩擦造成的磨损。表面硬化处理:表面硬化处理是提升机床床身表面硬度和耐磨性的重要手段。通过感应加热或渗碳氮化等方式进行局部硬化,使得床身表面形成硬质层,内层保持较好的韧性和塑性,从而达到内外兼修的效果。抛光与精磨:抛光是床身表面处理的关键步骤之一,通过机械或化学的方式去除工件表面粗糙度,使床身表面平滑细腻,减小摩擦阻力,利于导轨移动时的精确导向和减少振动。精磨则是进一步细化表面质量的过程,确保床身导轨面、安装面等重要部位的平面度、平行度和直线度符合严格的标准要求。对于大型机床床身铸件,除了轮廓尺寸大,壁厚也较大,因此所采取的工艺措施显得非常重要。
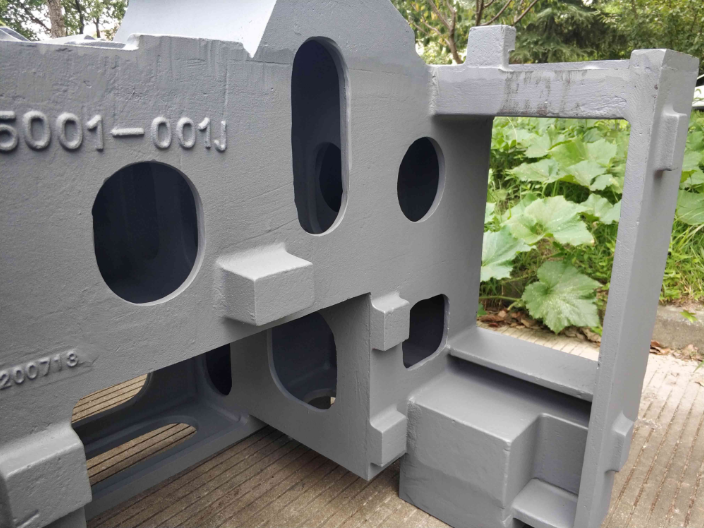
机床床身铸件尽可能选用底注包。底注包金属液的热损失小、压头大,渣子浮在金属液上表面,浇注钢水比较干净。受设备条件限制,对一些要求不高或一般中小机床床身铸件亦可用转包浇注。机床床身铸件浇注过程不可中断。在消失模铸件浇注时,保持连续地注入金属液,直至铸型全部充满。否则,就易在停顿处造成铸件整个平面的冷隔缺陷。机床床身铸件变形的原因:避免壁厚的突然改变。壁厚小又均匀的机床床身铸件采用同时凝固,壁厚大又不均匀的机床床身铸件采用由薄向厚的顺序凝固,合理的放置冒口的冷铁。渣气孔在机床床身铸件内部或者是表面形状不规则的孔眼。浇冒口不应该阻碍机床床身铸件收缩。机床床身退火种类:常见的退火工艺有:再结晶退火,去应力退火,球化退火,完全退火等。上海超精密机床床身铸件销售费用
直线导轨机床的高速度和高精度可以提高机床的加工效率。江苏机床床身铸件厂商
机床床身,通常被形象地比喻为机床的“骨骼”,是整个机床设备的主体支撑结构。它承载着机床的各个运动部件(如主轴箱、滑板、刀架等)以及工件的重量,同时承受切削力、夹紧力等各种动态载荷。因此,机床床身首先具备的主要功能就是承载和支撑。机床床身对于保证机床的几何精度具有决定性作用。床身的设计与制造精度直接影响到安装在其上的导轨、丝杠等传动部件的位置精度,进而影响机床的定位精度和重复定位精度。床身内部的筋板布局科学合理,能有效防止机床在工作过程中因受力变形而引起的精度下降,确保机床长期稳定的工作状态。江苏机床床身铸件厂商
上一篇: 杭州超精密机床床身铸件经销商
下一篇: 超精密机床床身铸件供应企业