复合管道软管材料规格尺寸
7.3.5管道内壁应光洁、平整、线性、无明显凸起;内衬管接口、接缝应平顺,新旧管道过渡应平缓;因施工原因产生的环形褶皱、纵向褶皱、局部隆起检查应符合下列规定:1局部划伤、磨损、气泡或干斑的出现频次每10m不应多于1处;2内衬管褶皱应满足设计要求;当设计无要求时,管道直线段比较大褶皱的高度不应大于0.02D或6mm中的较小值。检查方法:观察,检查CCTV检测图像。检查数量:全部检查。7.3.6内衬管道端部切口应平齐,应无松动、无明显贴合缝隙。检查方法:观察;检查施工记录。检查数量:全部检查。安庆UV-CIPP紫外线光固化软管生产厂家,就找江苏瑞斯曼新材料有限公司,质优价廉。复合管道软管材料规格尺寸
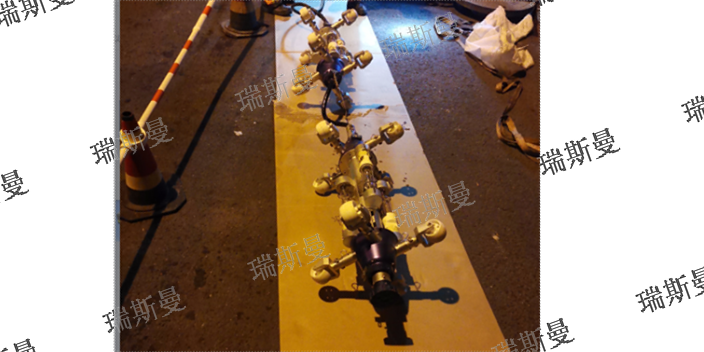
UV-CIPP紫外光固化技术就是将玻璃纤维编制成软管浸渍光固化树脂,然后将其拉入原有管道内充气扩张紧贴原有管道,以原有管道充当外模具,软管内膜为内模具,然后在管内使用紫外光的照射下使树脂固化形成具有一定强度的内衬管的管道修复加固方法。UV-CIPP管道紫外光固化修复材料:材料内含有光敏剂的聚酯、玻璃钢布以及其他数种树脂组合而成,在紫外光的照射下,通过光敏剂引发聚合反应,从而引起整个材料的固化,达到修复管道的目的。四川光固化软管材料参考价杭州UV-CIPP紫外线光固化软管生产厂家,就找江苏瑞斯曼新材料有限公司,质优价廉。
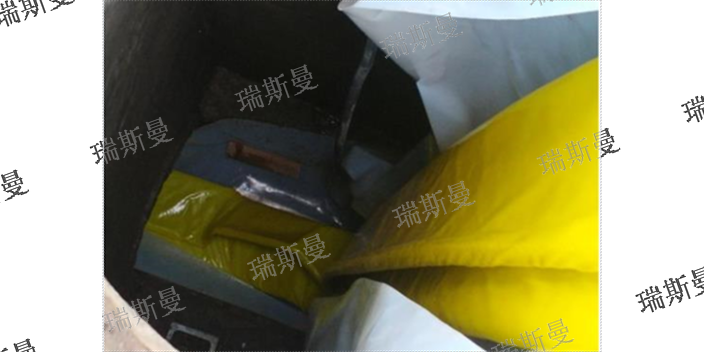
紫外光固化CIPP修复技术指的是在不改变待修复管道位置的条件下,先将浸透树脂的软管通过压缩空气充气膨胀方式,使软管与待修复管道内壁紧密贴合,再将紫外线灯放入充气的软管内,并控制紫外线灯在软管内以一定速度行走,使软管由一端至另一端逐步固化,紧贴待修复管道内壁,形成一层坚硬的“管中管”结构,从而使已发生破损或失去输送功能的地下管道在原位得到修复,是目前国际**的管道修复技术。紫外光固化CIPP修复技术指的是在不改变待修复管道位置的条件下,先将浸透树脂的软管通过压缩空气充气膨胀方式,使软管与待修复管道内壁紧密贴合,再将紫外线灯放入充气的软管内,并控制紫外线灯在软管内以一定速度行走,使软管由一端至另一端逐步固化,紧贴待修复管道内壁,形成一层坚硬的“管中管”结构
原管位固化修复在国外又简称CIPP树脂内衬修复,是在待修复的管道内壁上通过特殊载体(软管)衬一层液态的热固树脂,通过加热(热水、蒸汽或紫外线等)使其固化,形成与待修复管道紧密结合的管中管结构,从而提高管道的使用寿命,使用这项技术修复的管道寿命可达50年。CIPP全称为CuredInPlacePipe,意为原位固化法。以质量玻璃纤维缝编织物做基体材料,采用严谨科学的树脂体系,制作玻纤内衬软管。利用树脂吸热或遇光固化的原理,将固化前的玻纤内衬软管翻转或拉入待修复管道内部,用水或气将软管涨圆,再触发树脂的固化条件,使树脂在管道内固化,与原管道内壁紧密贴合,形成新的复合管道。江苏瑞斯曼新材料有限公司专营UV-CIPP紫外光固化软管,如有需要,欢迎来电沟通了解。
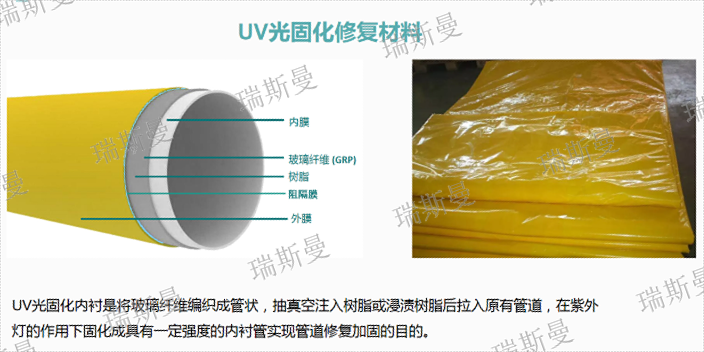
玻纤软管的拉入速度不应大于5m/min。5.3.5玻纤软管的许用牵拉力应按下式计算:(5.3.5)式中,F——许用牵拉力(kN);σ——管材的拉伸强度(MPa);k——许用牵拉力安全系数,可取2;D。——内衬管外径(mm);D₁——内衬管内径(mm)。当玻纤软管管径大于或等于DN800 时,玻纤软管拉入宜 采用送料平台辅助,当井口外玻纤软管的长度与检查井的深度接近时,应停止卷扬机,用扎带将玻纤软管尾部与牵引绳扎牢,并反向拉紧牵引绳,再次开启卷扬机,直至拉入完成。5.3.8拉入完成时,内衬软管两端应伸出原有管道。修复DN500及以下的管道,内衬管两端伸出原有管道的长度不应小于600mm;修复DN500以上的管道,内衬管两端伸出原有管道的长度不应小于1000mm。湖州UV-CIPP紫外线光固化软管生产厂家,就找江苏瑞斯曼新材料有限公司,质优价廉。四川非开挖管道软管材料生产厂家
六安UV-CIPP紫外线光固化软管生产厂家,就找江苏瑞斯曼新材料有限公司,质优价廉。复合管道软管材料规格尺寸
玻纤软管等进场材料应符合本规程第3.1节和3.2节的规定,产品合格证、质量保证书和产品性能检验报告应检查合格。检查方法:对照本规程第3.1节和3.2节检查。检查数量:全部检查。固化后应按设计要求取样,并应送第三方检测。内衬管短期力学性能应符合设计要求和本文件第3.3.1条的规定,苯乙烯含量测试应符合本文件第3.3.2条的规定,巴氏硬度测试应符合本文件第3.3.3条的规定,管壁的密实性应按本文件附录A进行测试。检查方法:现场切割取样、检测,全程应避紫外光。检查数量:同一生产厂家、同一加工批次、同一管径的产品现场取样不少于1组。复合管道软管材料规格尺寸
上一篇: 北京管道修复材料价格表
下一篇: 四川光固化软管材料参考价