四川高温直发器发热体材料
如果有多个直发器发热体发热板同时使用,则应采用并联方式代替串联。散热率的不同使直发器发热体的加热功率有较大的变化。开机后加热功率由高到低稳定。功率稳定性与使用条件有关,同一种直发器发热体,使用条件不同,则功率可相差好几倍。电子加热器热响应快,温度控制精确,综合热效率高。陶瓷加热器安性,低碳环保。电加热器本身的设计方案加温溫度在200摄氏下列的多级别,一切状况下本身均不泛红且有维护防护层,一切应用场合均不需要石棉等隔热材料进行降温处理,可放心使用不存在对人体烫伤和引发火灾的问题陶瓷加热器节约电能。陶瓷发热体元件是将电热体与陶瓷经过高温烧结,固着在一起。四川高温直发器发热体材料
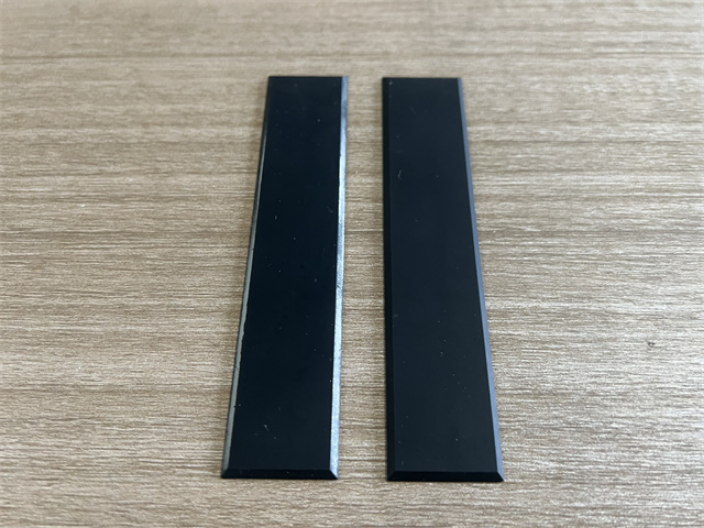
MCH高效环保节能陶瓷发热组件采用将发热电阻浆料按照发热电路设计的要求印刷于流延陶瓷生坯上,然后多层叠合共烧成一体,发热线路内置于陶瓷材料内,陶瓷体起到保护和绝缘的作用,从而具有耐腐蚀、耐高温、寿命长、高效节能、温度均匀、导热性能良好、热补偿速度快等优点,而且不含铅、镉、汞、六价铬、多溴联苯、多溴二苯醚等有害物质,是替代上述两种电热元件的理想产品。高效环保节能陶瓷发热片相比较PTC,在相同加热效果情况下节约20~30%电能。四川高温直发器发热体材料直发器发热体升温速度快,一般20秒到30秒可以使夹板表面温度达到200度。
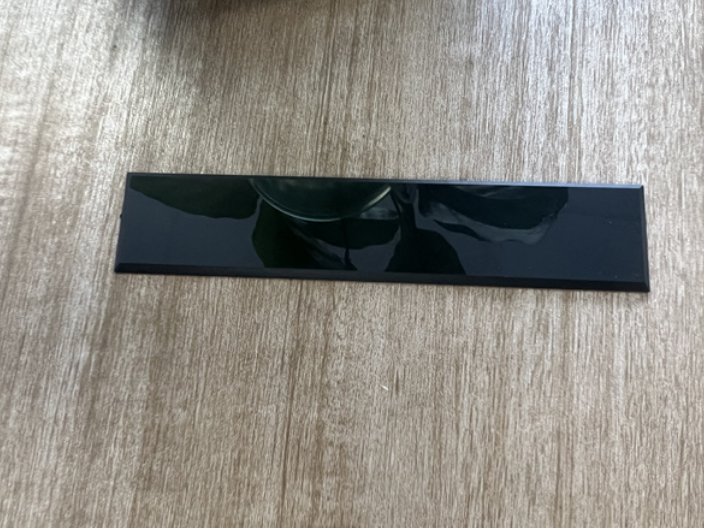
直发器发热体根据材质的不同,可分为氧化铝导热片、JRF氧化铝导热陶瓷片等等。直发器发热体用于需要导热、散热、绝缘、耐高温、耐高电压击穿的电子电气领域,热传导系数高,稳定性好。而氧化铝陶瓷片是一种高导热,高绝缘的一款材料。直发器发热体氧化铝含量高,结构比较致密,具有特殊的性能,故称为特种陶瓷。直发器发热体是以氧离子构成的密排六方结构,而铝离子填充于三分之二的八面体间隙中,这是与天然刚玉相同稳定的α-Al2O3结构,因此直发器发热体具有高熔点、高硬度,具有优良的耐磨性能。
直发器发热体与普通陶瓷发热体相比:在220V电压的情况下,直发器发热体比普通陶瓷发热体速度更快,相同功率下,直发器发热体比普通陶瓷发热元件更节能,直发器发热体不含铝材质,不会污染环境,目前氧化铝陶瓷发热体常见的有:陶瓷电热管、陶瓷发热盘、陶瓷发热片、陶瓷电热圈等,可根据应用场合的不同,选择不同的形状样式。它们的共同特点是电转换效率高、加热速度快、耐高温耐腐蚀、使用寿命长等。氧化铝陶瓷加热件,既符合环保要求、不含铅、镉、汞、多溴联苯、多溴二苯醚等有害物质,又有耐腐蚀耐高温、寿命长、高效节能等诸多优点,未来它一定能够有更普遍的应用。直发器发热体硬度大,耐磨性能极好,重量轻,适用范围广。
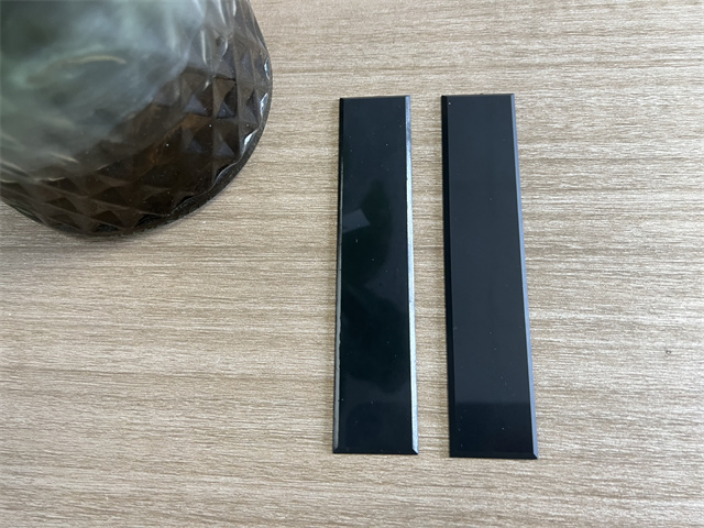
直发器发热体元件是将电热体与陶瓷经过高温烧结,固着在一起,直发器发热体是一种新型高效环保节能直发器发热体元件。直发器发热体具有耐腐蚀、耐高温、使用寿命长、高效节能、温度均匀、导热性好、热补偿快等优点。并且直发器发热体不含有铅、镉、汞、六价铬、多溴联苯、多溴二苯醚等有害物质。符合欧盟RoHS等环保要求。以高导热氧化铝瓷为基体,难熔金属为内电极,经一系列特殊工艺在1600℃共烧而成的高科技、高热、节能发热元件。氧化锆陶瓷化学性能比较稳定的无机非金属材料。浙江智能直发器发热体应用
直发器发热体由于使用时主要靠热传导,因此热效率高。四川高温直发器发热体材料
有一种直发器发热体采用的是黑色碳化硅陶瓷,它的特点是高温强度高直发器发热体,普通陶瓷材料在1200~1400摄氏度时强度将明显下降。而碳化硅陶瓷在1400摄氏度时抗弯强度仍保持在500~600MPa的较高水平直发器发热体,因此其工作温度可达1600~1700摄氏度。再加上碳化硅陶瓷的热传导能力也较高,在陶瓷中次于氧化铍陶瓷,直发器发热体因此碳化硅陶瓷已经应用于高温轴承、防弹板、喷嘴、高温耐蚀部件以及高温和高频范围的电子设备零部件等领域。四川高温直发器发热体材料
江苏佰特尔微电热科技有限公司坐落在祝塘镇新圩路59号,是一家专业的一般项目:技术服务、技术开发、技术咨询、技术交流、技术转让、技术推广;新材料技术研发;机械设备研发;电子元器件制造;机械电气设备制造;通用设备制造(不含特种设备制造);机械设备销售;电子元器件批发;金属材料销售;塑料制品销售;电气机械设备销售;电子产品销售(除依法须经批准的项目外,凭营业执照依法自主开展经营活动)公司。目前我公司在职员工以90后为主,是一个有活力有能力有创新精神的团队。江苏佰特尔微电热科技有限公司主营业务涵盖烘干设备发热体,即热式热水器,小厨宝,吹风机,坚持“质量保证、良好服务、顾客满意”的质量方针,赢得广大客户的支持和信赖。公司力求给客户提供全数良好服务,我们相信诚实正直、开拓进取地为公司发展做正确的事情,将为公司和个人带来共同的利益和进步。经过几年的发展,已成为烘干设备发热体,即热式热水器,小厨宝,吹风机行业出名企业。
上一篇: 陕西新款直发器发热体性能
下一篇: 天津绝缘MCH发热体寿命