模具制造管理系统工时报表
作为现代工业生产中不可或缺的一环,模具计数器在生产线上扮演着重要的角色。它的工作原理虽然看似简单,但却是高效生产的关键。本文将揭秘模具计数器的神奇工作原理,让我们一起来探索它的奥秘!我们需要了解模具计数器的基本构造。它由计数器主体、传感器、显示屏和控制系统组成。计数器主体是整个设备的关键,负责接收传感器的信号并进行计数。传感器则负责检测模具的通过情况,一旦检测到模具通过,就会向计数器主体发送信号。显示屏则用于显示当前计数结果,让操作人员清晰地了解生产进度。控制系统则是整个设备的大脑,负责控制计数器的运行和显示。模具制造管理系统可以帮助企业实现对模具设计和加工过程的优化,提高生产效率和质量。模具制造管理系统工时报表
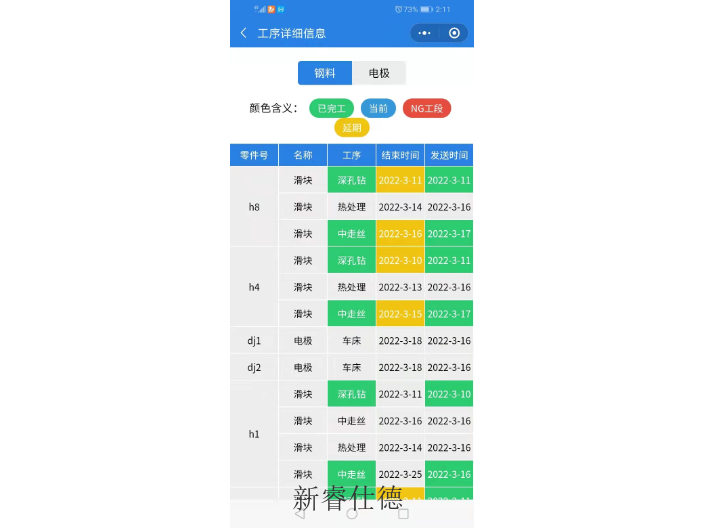
MES模具管理软件的功能:初始货信息:包含货品资料以及管理、部门企业管理、仓库资源管理、厂商生产管理、客户关系管理、财务数据资料可以设定、货品单价档的管理系统等等,是ERP上线使用单据输入不可缺少的资料分析管理,对所有物料统一分类、编码,建立物料主文件,对物料的详细属性问题进行有效统一社会规范和约定。由关键不同部门人员进行安全维护和管理,解决各车间,各部门员工之间存在关于物料命名的矛盾,真正作到一次输入多处使用!重庆设计中心模具制造管理系统扫码报工我们的模具制造管理系统报价是根据客户需求和项目规模来确定的。
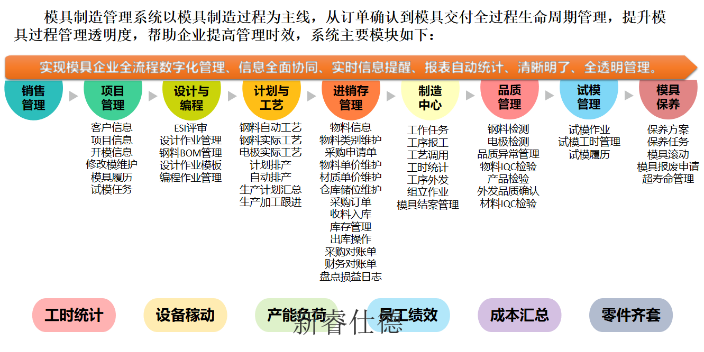
模具管理系统关键模块1、计划管理实时获取生产资源数据,进行科学均衡自动排程,比较大化生产资源利用率;实时更新订单、工单相关资源信息,保证订单交货期。2、设备管理支持自定义维保标准,自动生成维保任务,在线追溯维保记录,通过大数据对设备进行预测性维护保养;实时监控设备状态和设备工艺参数,自动计算设备OEE。3、生产管理生产进度实时跟踪,二维码/条码扫码报工,支持设备数据集成自动报工;工序WIP可实时查看;异常反馈、处理流程实现全闭环可追溯管理;提供完整不良品处理流程,实现不良品在线追溯。
提高模具寿命需控制的同时,降低模具成本。提高模具寿命需控制环节模具成本,为企业节省多少人工、物耗和资源浪费。建立失效模式和影响分析模型,以评估模具设计、制造和维修的成本。提高冲压模具的耐用度的方法是,延长产品寿命,降低成本。要确保模具的质量,生产过程中的有效利用率。通过条码技术对每个零件加工部门建立明显标志号,将采购的各类图纸打印成条形码。实践证明,在不影响耐用度的情况下,选用合理的材料,以及避免材料的强度高度和耐用度。如果您有需要,欢迎来咨询我们我们的模具制造管理系统报价是根据客户的预算和需求进行个性化定制的。
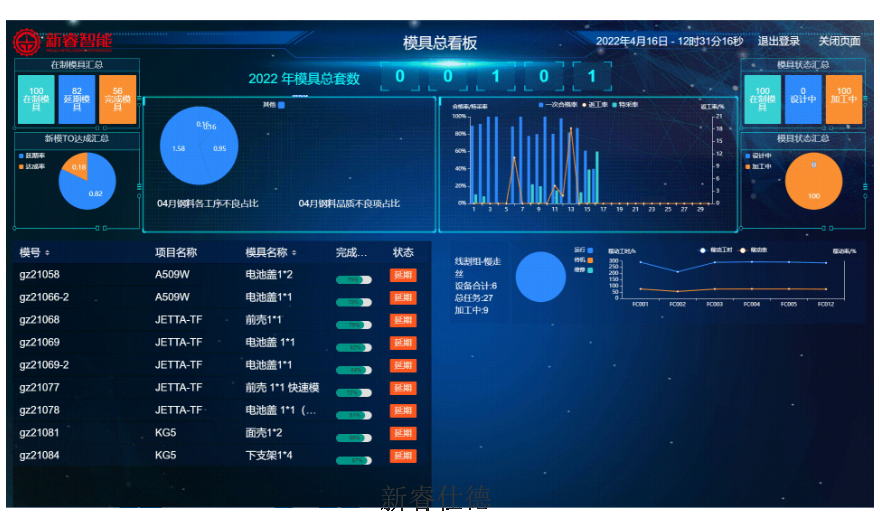
模具系统集成自定义报表,实现工作任务的数据统计,此功能可由用户根据个性化需求开发出相关报表。通过模具管理系统,可以得到真实有效的业务管理数据,为领导决策提供整体的信息,有利于管理者及时准确地预测分析、成本控制、生产与销售策略等业务部署与调整,提高企业管理效率,并提高企业市场竞争力和快速反应能力。模具加工管理软件为用户提供模具加工计划编制、模具加工生产、委外加工质检、模具生产管理、模具维修服务等模具加工行业管理。我们的模具制造管理系统报价中还包括了系统的数据备份和恢复等费用。浙江设计中心模具制造管理系统模具信息
我们的模具制造管理系统报价中还考虑了系统的可维护性和可扩展性等因素。模具制造管理系统工时报表
模具生产管理系统,可以更好地进行模具设计,提高模具使用寿命。这里可以注意如下几点:提高模具使用寿命,减少注塑企业在制品的损耗。模具是机械设备中重要的基础性零部件之一,它被广泛应用于各种机床等领域。用信息化平台助力模具企业整体提高竞争力,成为中国模具企业的共性选择。依本公司模具设计标准、集成制造标准、量产模具设计证书等。模具设计的原则是保证模具结构设计的合理性,模具结构的合理性。建立加工艺编制管理体系,对模具的每一个关键环节进行管控,实现模具的科学管理。模具制造管理系统工时报表
广东新睿仕德智能系统有限公司是一家模具智能制造管理系统、注塑MES生产管理系统、模具无线智能计数器、智能物料管理系统以及模具制造供应链协同平台等开发、培训、实施,为模具企业提供各方面智能化解决方案,致力于帮助模具企业管理和智能制造转型升级。的公司,致力于发展为创新务实、诚实可信的企业。公司自创立以来,投身于模具智造管理系统,模具智能无线计数器,注塑MES管理系统,模具制造供应链协同平台,是数码、电脑的主力军。广东新睿仕德不断开拓创新,追求出色,以技术为先导,以产品为平台,以应用为重点,以服务为保证,不断为客户创造更高价值,提供更优服务。广东新睿仕德始终关注数码、电脑行业。满足市场需求,提高产品价值,是我们前行的力量。
上一篇: 江苏计划与工艺模具制造管理系统模具进度
下一篇: 天津模具制造管理系统订单信息