辽宁试模管理模具制造管理系统模具进度
模具制造管理系统的实施是一个复杂而漫长的过程。在实施前,企业需要对自身的管理现状和业务流程进行各方面梳理和评估,明确系统的需求和目标。然后,企业需要选择合适的系统供应商和解决方案,制定详细的实施计划和时间表。在实施过程中,企业需要加强与系统供应商的合作和沟通,及时解决遇到的问题和困难。同时,企业还需要加强内部培训和宣传,提高员工对系统的认知度和使用水平。在应用方面,模具制造管理系统已经广泛应用于各类模具制造企业。通过应用该系统,企业能够实现对模具制造全过程的精细化管理和控制,提高生产效率和产品质量。例如,某模具制造企业通过引入模具制造管理系统,实现了对生产计划的自动排产和优化调整,提高了设备利用率和人员效率。同时,该系统还实现了对物料和质量的实时监控和追溯管理,确保了产品质量的稳定性和可追溯性。模具制造管理系统,实现数字化管理,提升生产效率。辽宁试模管理模具制造管理系统模具进度
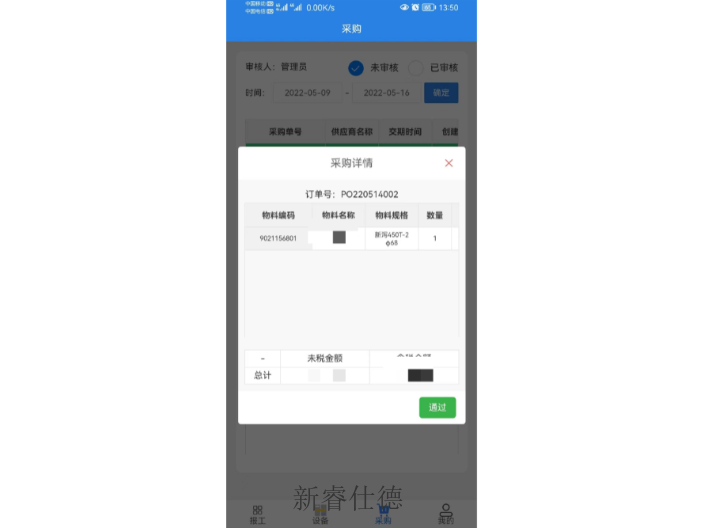
模具制造管理系统在提升决策效率方面也展现出了明显优势。通过收集和分析大量的生产数据,系统能够为企业的决策者提供准确、及时的信息支持。无论是生产计划的调整、设备采购的决策还是市场趋势的预测,系统都能够提供有力的数据支撑,帮助决策者做出更加明智的决策。在节能减排和绿色环保方面,模具制造管理系统也发挥了积极作用。系统通过对生产过程中的能耗和排放进行实时监控和统计分析,帮助企业识别节能减排的潜力并制定改进措施。例如,系统可以分析设备的能耗情况,提出合理的节能建议;同时,系统还可以对废弃物的产生和处理进行监控和管理,确保企业的生产活动符合环保要求。湖南品质管理模具制造管理系统工时报表数据分析驱动持续改进,不断优化生产流程。
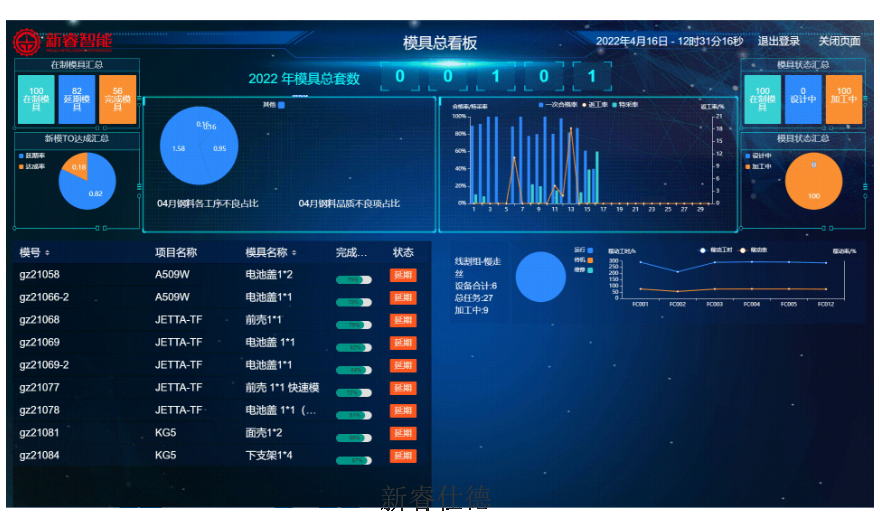
为了应对这些挑战和问题,我们需要从多个方面入手。首先,加强行业研究和交流,深入了解模具制造行业的实际需求和痛点问题,为系统设计和实施提供有力支持。其次,加强人才培养和引进力度,培养一支具备信息技术和管理知识的复合型人才队伍,为企业实施模具制造管理系统提供有力保障。此外,我们还需要加强与高校和科研机构的合作与交流,引进先进的技术和理念,推动模具制造管理系统的不断创新和发展。展望未来,随着信息技术和制造业的不断融合与发展,模具制造管理系统将迎来更加广阔的发展空间和机遇。首先,随着物联网、大数据、人工智能等技术的不断发展与应用,模具制造管理系统将实现更加智能化、准确化和个性化的管理与控制。
模具智能无线计数器,作为现代工业制造领域的一项创新技术,正逐渐改变着传统模具计数的方式。它融合了无线通信技术与智能算法,实现了模具使用次数的实时、远程监控,为企业的生产管理带来了改变性的变革。模具智能无线计数器的主要优势在于其无线传输功能。传统的模具计数器往往需要通过有线连接进行数据传输,这不仅限制了计数器的使用范围,还增加了布线和维护的复杂性。而智能无线计数器则通过无线通信技术,实现了数据的实时传输和远程监控,使得生产管理人员可以随时随地掌握模具的使用情况,无需受限于物理连接。协同工作平台促进团队沟通,加速问题解决。
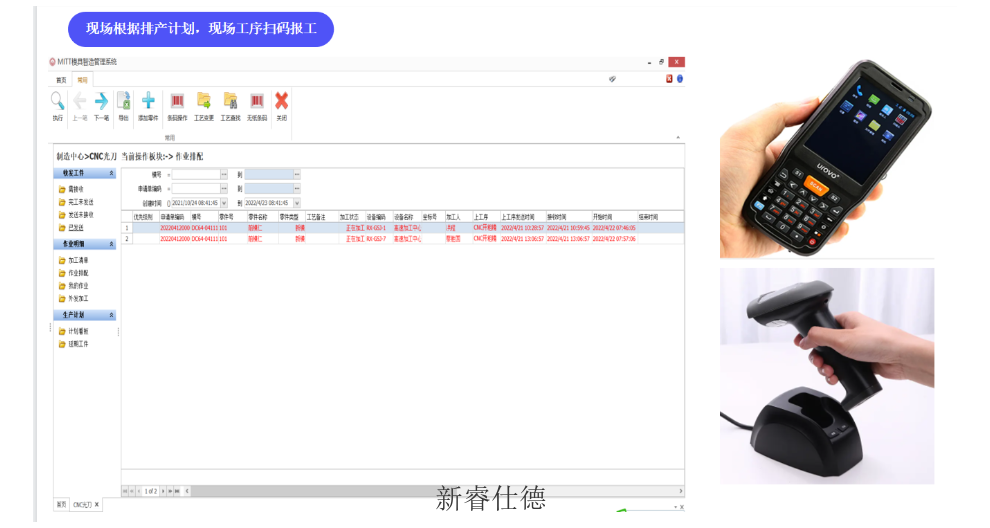
模具智造管理软件系统是现代模具制造企业不可或缺的工具,它能帮助企业提高生产效率,优化管理流程,降低成本。然而,要想充分发挥软件系统的效能,必须注意一些关键的使用事项。本文将探讨模具智造管理软件系统的使用注意事项,帮助企业更好地利用这一工具。一、数据安全与备份确保软件系统的数据安全是首要任务。定期备份重要数据,以防数据丢失或损坏。建议采用多种备份方式,如本地备份、云备份和外部硬盘备份,以确保数据安全可靠。强化网络安全防护,防止数据泄露和攻击。定期更新软件系统,安装新的安全补丁,使用可靠的防火墙和杀毒软件。灵活应对市场变化,模具制造管理系统助力企业快速响应。江苏项目管理模具制造管理系统工艺卡
智能化决策支持,为模具制造企业创造更大价值。辽宁试模管理模具制造管理系统模具进度
模具智能无线计数器的另一项重要功能是智能化管理。通过内置的智能算法和数据处理能力,计数器能够自动调整计数参数,适应不同模具的使用特点。同时,它还能够与其他智能化设备实现互联互通,构建完整的智能制造体系。在模具的库存管理方面,智能无线计数器也发挥着关键作用。通过无线通信技术,计数器能够将模具的库存信息实时传输至管理系统,使得库存管理人员能够准确掌握模具的数量和分布情况。这有助于优化库存结构,降低库存成本,提高库存周转率。此外,模具智能无线计数器还具备高度的灵活性和可扩展性。其无线通信模块支持多种通信协议,能够适应不同的网络环境。同时,计数器还支持软件升级和定制开发,能够根据企业的实际需求进行功能扩展和优化。辽宁试模管理模具制造管理系统模具进度