成都自动化电镀铜产线
电镀铜工艺短期将主要应用HJT和XBC电池领域,后续有望逐步向TOPCon电池导入。HJT电池利用本征非晶硅层将衬底与两侧掺杂非晶硅层完全隔开,通过高效钝化提升效率。光伏电镀铜基本可以分为水平电镀铜、VCP垂直电镀铜、龙门线电镀铜,电镀铜后采用的表面处理方式业界存在多种路线。主要工艺流程控制和添加剂在线路板行业使用时间久远技术已经成熟。电镀铜+电镀锡、电镀铜+化学沉锡、电镀铜+化学沉银几种路线。铜电镀工艺发展优势明显,较银浆丝网印刷具备更低的银浆成本、更优的导电性能、更好的塑性和高宽比,有望替代高银耗的丝网印刷技术,进一步提高电池效率和降低银浆成本,助力HJT和XBC电池降本增效和规模化发展。电镀铜工艺图形化:光刻路线和激光路线并行。成都自动化电镀铜产线
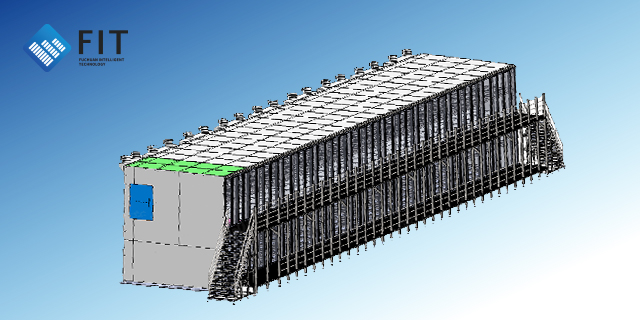
电镀铜优势在于可助力电池提效0.3-0.5%+,进而提高组件功率。相较于银包铜+0BB/NBB工艺,我们预计银包铜+0BB/NBB工艺或是短期内HJT电池量产化的主要降本路径,随着未来银含量30%银包铜浆料的导入,浆料成本有望降至约3分/W,HJT电池金属化成本或降至5分/W左右。电镀铜工艺有望于2023-2024年加快中试,并于2024年逐步导入量产。随着工艺经济性持续优化,电镀铜HJT电池的金属化成本有望降至5-6分/W左右,叠加考虑0BB/NBB对应组件封装/检测成本提升,而电镀铜可提升效率约0.5%+,电镀铜优势逐渐强化,有望成为光伏电池无银化的解决方案。浙江光伏电镀铜设备费用电镀铜可以提高金属的抗腐蚀性和耐磨性,延长其使用寿命。
光伏铜电镀技术采用金属铜完全代替银浆作为栅线电极,实现整片电池的工艺转换,打破瓶颈,创新行业发展。光伏电镀铜设计的导电方式主要有弹片式导电舟方式、水平滚轮导电、模具挂架式、弹片重力夹具等方式。合理的导电方式对光伏电镀铜设备非常重要是实现可量产的关键因素之一。优良的导电方式可以实现设备的便捷维修和改善电镀铜片与片之间的电镀铜厚极差,甚至可以实现单片硅上分布电流的可监控性。太阳能电池电镀铜技术。这项技术不仅可提升太阳能电池板效能,而且可大规模降低成本。以开掘市场潜力,全新的电镀工艺旨在进一步针对低成本电池的需求。
光伏电镀铜基本可以分为水平电镀铜、VCP垂直电镀铜、龙门线电镀铜,电镀铜后采用的表面处理方式业界存在多种路线。主要工艺流程控制和添加剂在线路板行业使用时间久远技术已经成熟。电镀铜+电镀锡、电镀铜+化学沉锡、电镀铜+化学沉银几种路线。釜川,以半导体生产设备、太阳能电池生产设备为主要产品,打造光伏设备一体化服务。拥有强大的科研团队,凭借技术竞争力,在清洗制绒设备、PECVD设备、PVD设备、电镀铜设备等方面都有独特优势;以高效加工制造、快速终端交付的能力,为客户提供整线工艺设备的交付服务。 电镀铜技术路线是对传统丝网印刷环节的替代,可以分为“种子层制备 +图形化+金属化+后处理”四大环节。
光伏电池是光伏系统实现光电转换的重要的器件,其制备流程主要分为清洗制绒、扩散制结、正背面镀膜、金属化印刷固化等几大工艺环节。其中,金属化环节主要用于制作光伏电池电极栅线,通过在电池两侧印刷银浆固化金属电极,使得电极与电池片紧密结合,形成高效的欧姆接触以实现电流输出。金属化环节主要有银浆丝网印刷、银包铜丝印、激光转印、电镀铜、喷墨打印等几类工艺,传统的丝网印刷成熟简单是目前主流量产技术路线,其他工艺尚未实现大规模产业化。电镀铜具有良好的抗冲击性和抗划痕性,可以在各种环境下保持金属的光泽和完整性。浙江光伏电镀铜设备费用
电镀铜技术路线湿膜光刻比干膜光刻多一道烘烤环节,但其性能优异和成本低,为目前主流路线。成都自动化电镀铜产线
铜栅线更细,线宽线距尺寸小,发电效率更高。栅线细、线宽线距小意味着栅线密度更大,更多的栅线可以更好地将光照产生的内部载流子通过电流形式导出电池片,从而提高发电效率,铜电镀技术电池转化效率比丝网印刷高0.3%~0.5%。①低温银浆较为粘稠,印刷宽度更宽。高温银浆印刷线宽可达到20μm,但是低温银浆印刷的线宽大约为40μm。②铜电镀铜离子沉积只有电子交换,栅线宽度更小。铜电镀的线宽大约为20μm,采用类半导体的光刻技术可低于20μm。成都自动化电镀铜产线
上一篇: 成都双面微晶异质结PVD
下一篇: 广东HJT