武汉机箱支架铝合金压铸厂商
铝合金压铸以其独特的工艺和卓著的性能特点,成为现代制造业中不可或缺的一环。铝合金压铸件不只具有优异的机械性能,如高的强度、高韧性,还具备比较好的导热性和耐腐蚀性。此外,铝合金压铸件的尺寸精度高,表面质量良好,能够满足各种复杂结构的设计需求。这种独特的优势使得铝合金压铸在电子、汽车、家电等行业得到普遍应用。铝合金压铸技术历经数百年的发展,从较初的铅字铸造到如今的精密压铸,每一步都凝聚着人类的智慧和努力。自19世纪以来,压铸技术不断进步,尤其是铝合金压铸技术的发展,为现代制造业带来了改变性的变革。如今,铝合金压铸已成为制造业中不可或缺的一部分。铝合金压铸件,耐用又美观。武汉机箱支架铝合金压铸厂商
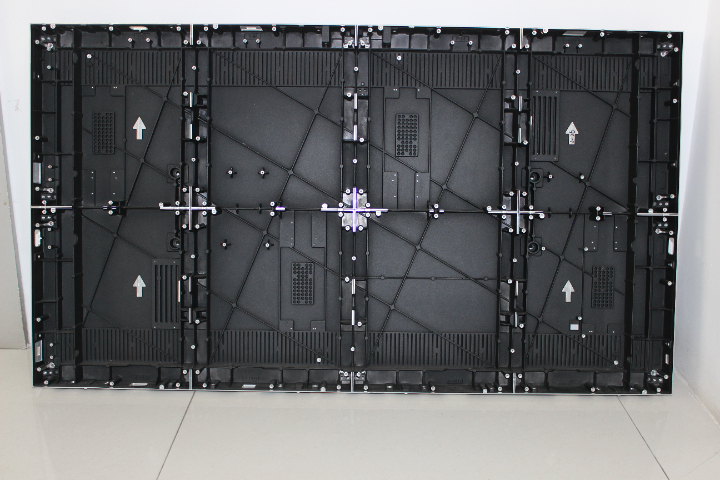
在汽车行业中,铝合金压铸产品同样发挥着重要作用。随着汽车轻量化趋势的加速推进,铝合金压铸技术成为实现汽车轻量化的重要手段之一。铝合金压铸产品被普遍应用于汽车发动机、底盘、车身等部件的制造中,不只减轻了汽车的重量,还提高了汽车的燃油经济性和安全性。此外,铝合金压铸技术还可以实现复杂形状和结构的制造,为汽车设计提供了更多的可能性。在电机行业中,铝合金压铸产品也有着普遍的应用。电机是许多设备和系统中的重要组成部分,对材料的要求非常高。铝合金压铸产品具有轻质、高的强、导热性好等特性,能够满足电机对材料的要求。同时,铝合金压铸技术还可以实现高精度、高效率的生产,为电机制造提供了好质量的材料支持。例如,在风力发电、电动汽车等领域中,铝合金压铸产品被普遍应用于电机的制造中。山东振子铝合金压铸制造铝合金压铸,高效节能,环保优先选择。

铝合金压铸行业在市场竞争中面临着诸多挑战。一方面,随着国内外市场的不断开放和竞争的加剧,企业需要不断提高产品质量和服务水平以满足客户的需求;另一方面,原材料价格的波动和环保政策的收紧也给企业带来了不小的压力。因此,企业需要加强市场调研和产品开发力度,提高产品的附加值和竞争力;同时加强内部管理和成本控制,降低生产成本和提高经济效益。铝合金压铸行业的发展趋势是向着智能化、绿色化和国际化的方向发展。随着人工智能和物联网等技术的不断发展和应用,铝合金压铸行业将实现生产过程的智能化和自动化控制;同时,随着环保意识的提高和可持续发展理念的普及,企业也将更加注重绿色生产和环境保护;此外,随着国际市场的不断开放和竞争的加剧,铝合金压铸行业也将积极参与国际竞争和合作,推动行业的国际化和全球化发展。
Zn2+作为磷化液中的另一种重要添加剂,对铝材磷化过程也有着卓著的影响。研究表明,当Zn2+浓度较低时,不能形成有效的磷化膜或磷化膜质量较差。随着Zn2+浓度的增加,膜重逐渐增加,磷化膜的质量也得到改善。但是,过高的Zn2+浓度会导致磷化膜过厚、粗糙,降低其耐腐蚀性和附着力。因此,在铝材磷化过程中,需要合理控制Zn2+的添加量以获得高质量的磷化膜。PO4含量是铝材磷化过程中的另一个关键因素。研究表明,PO4含量对磷化膜重有着卓著的影响。提高PO4含量可以增加磷化膜的膜重,使其更加致密、耐腐蚀。但是,过高的PO4含量也会导致磷化液中的磷酸盐浓度过高,影响磷化膜的质量和性能。因此,在铝材磷化过程中,需要严格控制PO4的含量以获得高质量的磷化膜。铝合金压铸,打造轻量化新选择。

铝合金压铸的工艺流程包括模具设计、熔炼、压铸、冷却和后续处理等多个环节。模具设计是压铸生产的关键环节之一,它决定了压铸件的形状和尺寸精度。熔炼是将铝合金材料加热至熔化状态,为压铸提供合格的液态金属。压铸是将液态金属注入模具中,经过冷却凝固后形成压铸件。后续处理包括去毛刺、热处理、表面处理等工序,以改善压铸件的性能和外观质量。在电子行业,铝合金压铸技术发挥着重要的作用。由于电子产品对零件的尺寸精度和表面质量要求非常高,因此铝合金压铸技术成为了电子行业的重要生产工艺之一。铝合金压铸件在电子产品中普遍应用于散热器、外壳、支架等部件的生产,为电子产品的稳定性和可靠性提供了有力的保障。铝合金压铸件,轻巧坚固,使用寿命长。武汉机箱支架铝合金压铸厂商
压铸铝合金,耐用且稳定。武汉机箱支架铝合金压铸厂商
Zn2+作为磷化液中的重要成分,其浓度对磷化膜的质量有着卓著影响。当Zn2+浓度较低时,磷化膜难以形成或质量较差。随着Zn2+浓度的增加,磷化膜的重量也逐渐增加。然而,过高的Zn2+浓度也可能导致磷化膜质量的下降。PO4含量是磷化液中另一个关键因素。研究表明,提高PO4含量可以卓著增加磷化膜的重量。这是因为PO4是磷化膜的主要成分之一,其含量的增加可以促进磷化膜的形成和生长。然而,过高的PO4含量也可能导致磷化膜质量的下降。因此,在铝合金压铸过程中需要严格控制PO4的含量。武汉机箱支架铝合金压铸厂商
上一篇: 山东通信配件压铸模具工艺
下一篇: 上海铜精密压铸公司