山东供应超声波液体处理调试
工艺流程:
一般来说,清洗的工艺流程依被清洗物体清洗的难易程度及清洗数量而决定。主要清洗流程如下:
1)热浸洗或喷洗:目的是将工件上的污染物软化、分离、溶解,并减轻下道清洗工序的负荷。
2)超声波清洗:利用超声波产生的强烈空化作用及振动将工件表面的污垢剥离脱落,同时还可将油脂性的污物分解、乳化。
3)冷漂洗:利用流动的净水将已脱落但尚浮在工件表面上污物冲洗干净。
4)超声波漂洗:溶剂为干净的清水,工件浸入后,利用超声波将浮在工件各边、角及孔隙处的污物清洗干净。
5)热净水及冷净水漂洗:进一步去除悬附在工件表面上的污物微粒。
6)热风烘干:利用一定的温度和风速,使零件表面快速干燥。 利用超声波液体处理技术可以有效地去除水中的有机物和无机盐类。山东供应超声波液体处理调试
超声波液体处理
4)槽液循环过滤系统。在该系统中设有过滤器,对槽液进行动态过滤,以维持槽液的清洁度。当工件出槽,经过过滤的液体流经槽体上部的喷淋环节对工件进行一次冲洗,以便冲掉工件出槽时表面粘附的油污,以避免其对下道槽液造成污染。
5)输送系统:根据被清洗工件的形状、体积、批量等确定超声波清洗机的输送方式及控制方式。
6)喷淋漂洗系统:根据被清洗工件的表面状况,有的清洗机配备喷淋漂洗工序,将超声波清洗和喷淋清洗有机地结合起来。
7)烘干系统:根据被清洗工件的状况,有的清洗机配备烘干系统,烘干系统主要由加热器、风机、吹风喷嘴等组成温度自动控制。 广东通用超声波液体处理市场价利用强超声波进行液体处理时,会产生空化效应和声流效应。
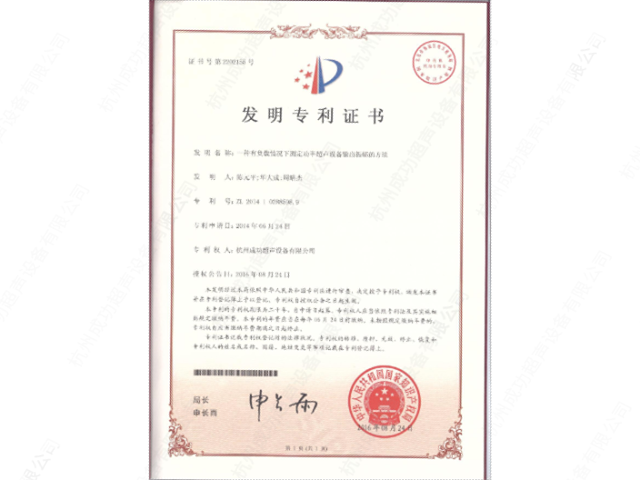
超声波细胞破碎仪是一种环保的细胞破碎设备,它能够快速破碎细胞壁,释放出细胞内部物质。在生物医药、食品、环保等领域得到广泛应用。而制备乳化液是超声波细胞破碎仪的一个重要应用方向,它可以制备出均一稳定、粒径分布均匀的乳化液。本文将介绍超声波细胞破碎仪制备乳化液的原理、工艺流程及实验方法。
超声波细胞破碎仪制备乳化液的原理主要是利用超声波的空化效应。当超声波在液体中传播时,会产生交替的压缩和拉伸区域,当声强达到一定值时,会在液体中产生空化泡。这些空化泡在声波的振动作用下不断生长、收缩、崩溃,产生强烈的微射流和冲击波,从而破坏细胞壁,释放出细胞内部物质。同时,超声波的振动作用还可以使液体产生激烈的搅拌,促进乳化液的形成。
超声波声化学:
超声波液体处理设备在强度超声下的液体会发生超声空化。它可以被看作是在超声波工具头附近形成的一团气泡云,听起来是一种强烈的嘶嘶声。空化产生剧烈的、不对称内爆的真空气泡,引起具有极强机械剪切力的微射流。这些力就是超声波驱动许多物理和化学过程前进的能力。超声波能量作用于介质,会引起质点高速细微的振动,产生速度、加度声压、声强等力学量的变化,作用于提取、破碎、乳化、分散、消泡、消泡、消泡等。 超声波液体处理可以用于制备高分子材料,如聚酰亚胺膜等。
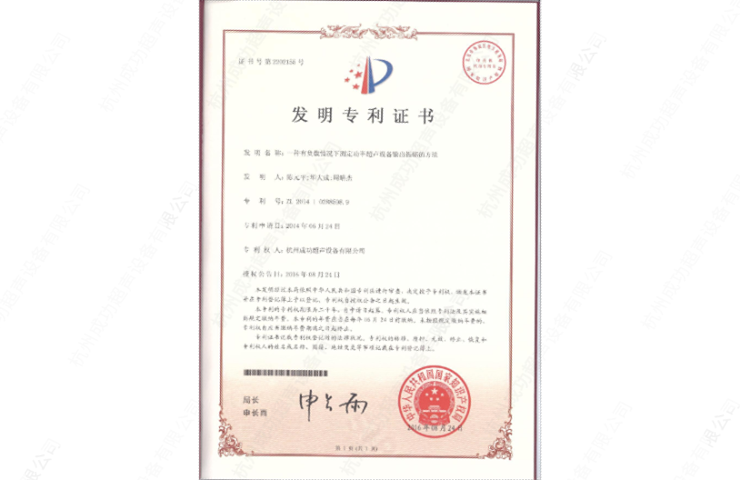
稳定的水包油乳液非常难以分离并且是石油生产过程中遇到的困难的问题之一。乳液粘度远高于分离相的粘度,这是井筒压降高、油藏采收率低的原因。本文关于使用超声波能量来增强悬浮油相与水介质分离的实验室研究。本文研究了超声波能量对稳定的水包油乳液中油水分离的影响。研究发现,油相浓度、油相组成、超声强度和温度是影响乳液聚结的关键因素,乳液聚结发生在超声处理后相对较短的时间内。此外,油滴具有较高的油相组成(10%,35%),这可能是对过去研究工作中观察到的残油减少的解释。拍摄了许多动态聚结过程的显微照片,并记录了平均液滴尺寸的变化。这导致建立了聚结速率的数学模型,该模型是超声频率、油相浓度和其他变量的函数。这些模型理论上是健全的,易于使用。数学模型预测与实验结果的比较提供了很好的一致性。超声波液体处理可以用于制备微胶囊、微球等微粒。上海销售超声波液体处理维修
超声波液体处理可以应用于各种液体,包括水、油、化学品等。山东供应超声波液体处理调试
超声波乳化脱气仪优势:1、可以制造高质量的乳液能够获得体积小(只有0.2~2μm)和液滴尺寸分布窄(0.1~10μm)的乳液液滴,它还可以增加浓度高达30%,甚至在乳化剂配合下可以高达70%浓度。2、乳化效果稳定使用少量乳化剂或不使用乳化剂,可获得稳定的乳液。超声波处理后的乳化液可保持数月或半年以上的稳定性。3、超声波乳化可控制乳化液的种类在一定条件下,超声波方法可以生成油包水和水包油。就力学方法而言,乳化剂的性质决定乳化液的类型。而在不同的声强下,会产生不同类型的乳液。4、创造*的乳液超声乳化还可以制备出一般方法不能制备的乳状液。例如,常用的混合方法只能在水中产生5%的石蜡乳液,而不可思议的是,在功率超声场的作用下可以产生20%的石蜡乳液。山东供应超声波液体处理调试
上一篇: 福建耐用超声波液体处理批量定制
下一篇: 浙江直销超声波雾化销售厂家