西门子数控系统维修中心
事例:故障现象:一加工中心,开机后打开急停,系统在复位的过程中,伺服强电上去后系统总空开马上跳闸。故障分析:该加工中心使用国产数控系统,经对故障进行了检查分析,首先怀疑是否是空开电流选择过小,经过计算分析后确认所选择的空开有点偏小,但基本符合机床要求,然后用示波器观察机床上电时的电流的变化波形,发现伺服强电在上电时电流冲击比较大,也就是电流波形变化较大,进一步分析发现由于所选伺服功率较大,且伺服内部未加阻抗等装置,在使用时须外接一电抗与制动电阻,电气人员在设计时加了制动电阻,为了节省成本没有使用阻抗。按照要求加上阻抗后,系统上电恢复正常。打包设备发格FAGOR数控系统常见故障维修.西门子数控系统维修中心
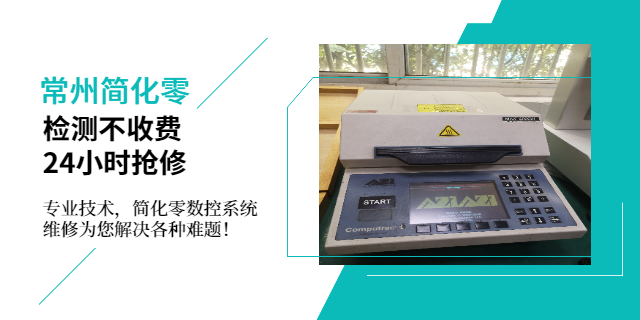
硬件故障是数控系统维修中较为复杂的问题之一。硬件包括主板、CPU、内存、硬盘、显卡等组件。其中,主板上的芯片损坏、电容漏电,内存的接触不良或损坏,硬盘的坏道、分区表错误,以及显卡的故障等都可能导致系统无法正常启动或者运行异常。比如,在一家模具加工厂,一台数控铣床出现开机后屏幕无显示的情况。经过仔细检查,发现是主板上的一个显示芯片出现了虚焊,导致显卡无法正常工作。通过重新焊接芯片,解决了显示问题,使铣床恢复正常运行。西门子数控系统维修中心维修人员在拆卸数控系统部件时,要做好标记,便于安装时准确无误。
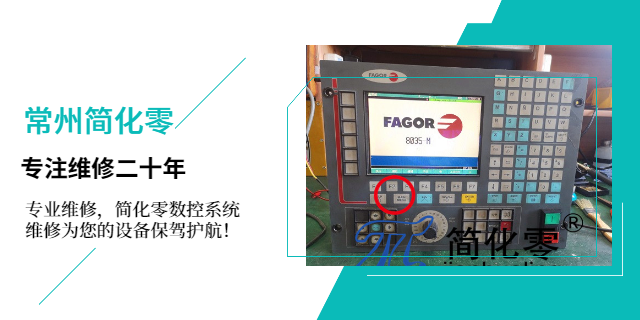
25050 轮廓监控,轮廓误差大于轮廓监控公差带,即轮廓误差大于MD36400设定值 1.增大轮廓监控公差带MD36400设定值 2.对位置环和速度进行优化 3.提高增益MD32200设定值 4.减小加速度MD32300设定值 5.检查机械部分 25060 速度设定值点限制,指令速度大于****大速度设定值,即速度设定值大于MD36210中的数值 1.检查速度的实际值是否受到机械部件运动的影响 2.检查速度设定值电缆 3.修改****大速度MD36210和设定值监控延迟时间MD36220 25070 轴的漂移太大 通过关闭自动补偿,调节偏移补偿,知道位置滞后为零,然后再恢复自动补偿以便平衡动态漂移变化 25080 轴的位置监控,跟随误差大于精确****停设定值,即跟随误差大于MD36010的设定值 1.适当增加精确准停限制MD3600,MD36010 2.增加****停时间MD36020 3.优化速度/位置调节器,提高伺服增益MD32200
数控系统作为现代制造业中关键的设备控制中心,其稳定运行对于生产效率和产品质量至关重要。然而,如同任何复杂的电子设备一样,数控系统也可能会出现故障,需要进行及时有效的维修。以下将为您详细阐述数控系统维修的相关说明。数控系统的维修工作首先需要对其基本结构和工作原理有深入的了解。数控系统通常由硬件和软件两大部分组成。硬件包括中心处理器、存储器、输入输出接口、驱动电路等;软件则包含操作系统、控制程序、驱动程序等。当系统出现故障时,维修人员需要迅速判断是硬件问题还是软件问题。例如,在一家机械加工厂,一台数控机床突然出现停机故障。维修人员首先检查了电源供应,确保硬件部分有稳定的电力输入。然后,通过查看系统的报错信息和运行日志,初步判断可能是控制程序出现了异常。经过进一步的软件调试和更新,成功解决了问题,使机床恢复了正常运行。 发格数控系统M系列报警9107/9108维修.
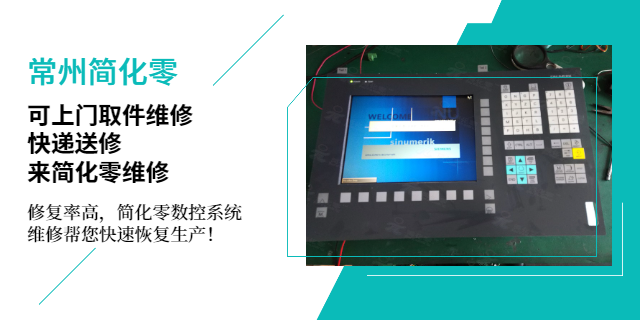
在一家船舶制造企业,一台数控等离子切割机在切割过程中突然停止,且无法重新启动。维修人员检查了电源、控制系统和切割头,均未发现明显故障。通过查看系统的故障报警记录,发现是由于过载保护触发导致停机。进一步检查发现,切割头的磨损严重,导致切割阻力增大,从而引发过载。更换切割头并重新设置过载保护参数后,数控等离子切割机恢复正常运行。这个案例提醒我们,在维修过程中,要充分利用系统的故障报警信息,结合实际情况进行分析和判断。对于无法确定的数控系统故障,可以采用替换法逐步排除可能的故障部件。西门子数控系统维修中心
维修人员要不断总结数控系统维修的经验教训,提高自身的技术水平。西门子数控系统维修中心
在进行数控系统维修之前,充分的准备工作是必不可少的。这包括收集故障相关的信息,如故障发生的时间、现象、操作过程等。同时,准备好必要的维修工具和检测设备,如示波器、万用表、编程器等。对于一些常见的故障现象,维修人员应有一定的经验和预判能力。比如,系统频繁死机可能是由于散热不良导致的硬件过热;而加工精度突然下降则可能与驱动电机或编码器的故障有关。以某汽车零部件生产企业为例,一台数控加工中心出现加工尺寸偏差的问题。维修人员在到达现场后,首先与操作人员沟通,了解故障前后的加工工艺和参数设置。然后,使用量具对加工件进行测量,确定偏差的具体数值和规律。通过这些准备工作,为后续的准确诊断和维修奠定了基础。西门子数控系统维修中心
上一篇: 汇川伺服驱动器故障检测与维修哪家好
下一篇: 丹阳可编程控制系统工控机维修中心