耐用电刷镀技术
工件表面的预处理情况对镀层质量有着基础性的影响。在电刷镀之前,工件表面必须进行彻底的清洗、除锈和活化处理。若工件表面残留有油污、油脂等有机污染物,会阻碍镀液与工件表面的有效接触,导致镀层附着力不佳,甚至出现起皮、剥落等问题。同样,表面的铁锈和氧化皮若未去除干净,会影响金属离子在工件表面的沉积,使镀层与基体之间的结合力降低。而活化处理能够在工件表面形成一层微观上粗糙且活性高的表面层,有利于增强镀层与基体的结合力。镀液成分准确调配,是电刷镀镀层质量好的关键保障。耐用电刷镀技术
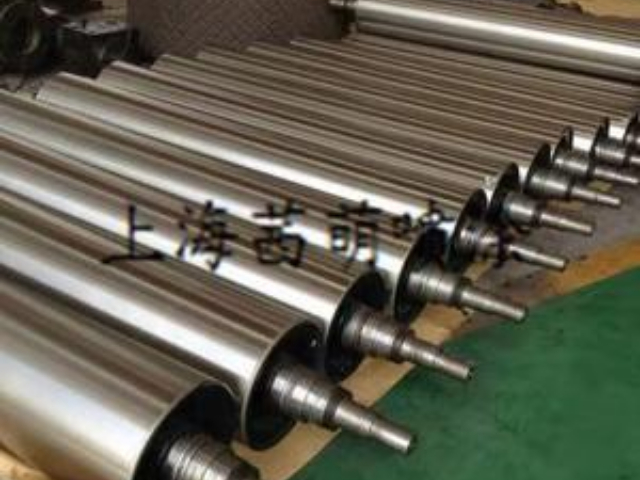
高度的灵活性与针对性
传统电镀通常需要将工件完全浸没在镀槽中进行整体镀覆,对于一些大型工件或只需局部镀覆的情况,操作极为不便。而电刷镀通过镀笔与工件的局部接触来实现镀覆,操作人员可以根据实际需求,准确地对工件的特定部位进行处理。例如,当机械零件只局部出现磨损或腐蚀时,电刷镀能够只对受损区域进行镀覆修复,避免了对整个零件进行不必要的处理,很大程度提高了处理效率,同时减少了对零件其他正常部位的影响。这种灵活性是传统电镀以及其他一些表面处理技术难以企及的,热喷涂等技术往往会对较大面积的表面进行覆盖,难以实现如此准确的局部处理。 浙江加工电刷镀共同合作电刷镀特殊功能镀液,赋予镀层自润滑等特性。
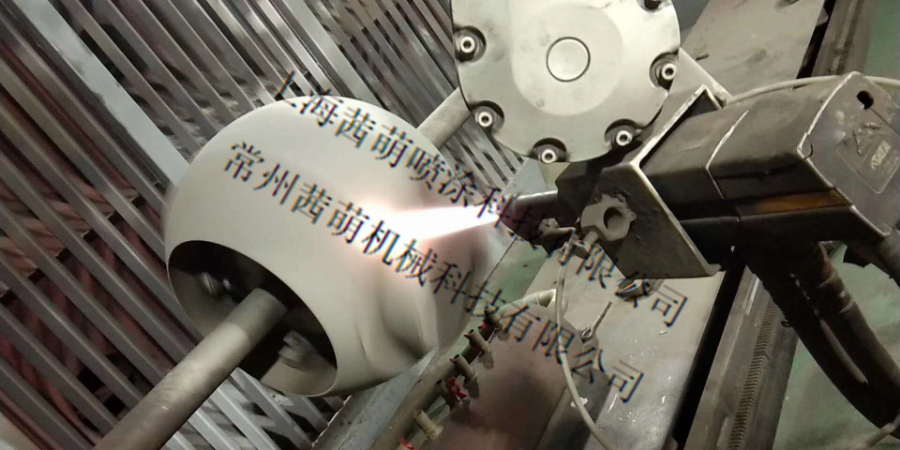
从阳极的设置来看,传统电镀通常采用大面积的可溶性阳极,如在镀铜工艺中,阳极一般为铜板。在电镀过程中,阳极铜板不断溶解,释放出铜离子进入镀液,以此补充镀液中被消耗的铜离子,维持镀液成分的相对稳定。这一过程中,阳极铜板的溶解速率与阴极工件上铜离子的沉积速率需要达到一定的平衡,以确保镀层质量和镀液性能。而电刷镀的阳极则采用不溶性材料,常见的是石墨。石墨阳极本身不参与化学反应、不会溶解,其主要作用是传导电流。镀笔的阳极部分包裹着吸附镀液的棉花等材料,通过镀笔与工件的接触,将镀液中的金属离子输送到工件表面。这种阳极设置方式使得电刷镀在操作上更加灵活,无需像传统电镀那样频繁更换阳极材料,也避免了阳极溶解产物对镀液的污染。
电刷镀过程中的工艺参数,如电流密度、电压、镀笔移动速度等,对镀层质量有着直接且紧密的联系。电流密度决定了单位时间内通过单位面积的电荷量,进而影响金属离子的沉积速率。当电流密度过低时,镀层沉积缓慢,结晶细致但可能导致镀层厚度不均匀;而电流密度过高,会使金属离子在阴极表面的还原反应过于剧烈,容易产生气孔、烧焦等缺陷,同时镀层的内应力增大,可能导致镀层开裂。
电压作为驱动电流的动力源,与电流密度密切相关。一般来说,提高电压会使电流密度增大,但过高的电压可能引发镀液的电解副反应,产生氢气和氧气。氢气的析出会在镀层中形成气孔,降低镀层的致密性;氧气的产生则可能氧化镀液中的某些成分,破坏镀液的稳定性,进而影响镀层质量。
镀笔移动速度也是影响镀层质量的重要参数。镀笔移动速度过快,镀液与工件表面的接触时间过短,金属离子来不及充分沉积,导致镀层厚度不均匀,甚至出现漏镀现象;移动速度过慢,则会使局部镀层过厚,可能造成镀层与基体之间的结合力下降,并且浪费镀液。 电刷镀在机械制造,修复磨损轴类效果明显。
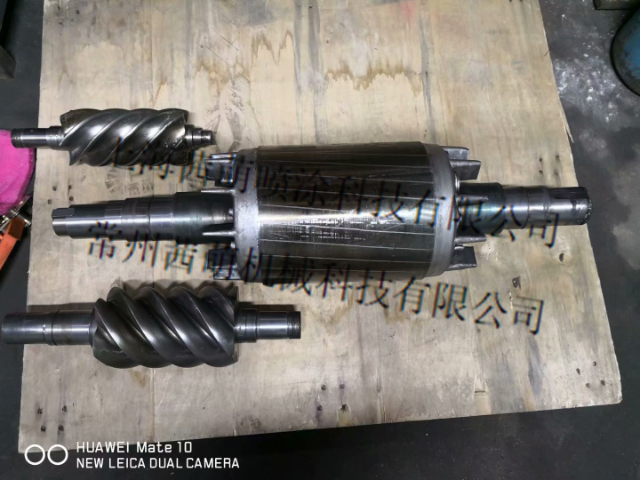
镀笔的移动速度同样不容忽视。镀笔移动过快,镀液与工件表面的接触时间过短,金属离子来不及充分沉积,容易造成镀层厚度不均匀;而镀笔移动过慢,则可能导致局部金属离子过度沉积,镀层过厚,影响镀层的整体性能。镀液的成分、酸碱度以及工件表面的预处理情况等,都会对金属在物体表面的沉积效果产生影响。合适的镀液成分能够为金属离子提供稳定的存在环境,适宜的酸碱度有助于维持镀液的化学平衡,而良好的工件表面预处理能够确保镀层与基体之间具有良好的附着力。电刷镀设备简单,便于携带至现场进行处理。山东哪里有电刷镀报价
电刷镀操作时,镀笔与工件接触压力要适中。耐用电刷镀技术
镀液作为电刷镀过程中金属离子的来源与反应介质,其成分与性质对镀层质量起着决定性作用。首先,镀液中金属离子的浓度是关键因素之一。若金属离子浓度过低,单位时间内迁移到阴极(工件)表面的离子数量不足,导致镀层沉积速率缓慢,不仅生产效率低下,还可能使镀层结晶不致密,出现孔隙等缺陷。相反,过高的金属离子浓度会使沉积反应过于剧烈,金属原子来不及有序排列,造成镀层结晶粗糙,甚至产生树枝状结晶,严重影响镀层的外观与性能。耐用电刷镀技术
上一篇: 天津多功能纳米陶瓷涂覆施工
下一篇: 泰州防腐轴修复施工