南京锯片磨床动静压主轴
对静压主轴轴承、丝杆螺母副、高速运动的导轨副等不能分离的热源,从结构、润滑等方面改善其摩擦特性,减少发热或用隔热材料;采用强制式风冷、水冷等散热措施。均衡温度场加速达到传热平衡,控制环境温度,加工原理误差是指采用了近似的刀刃轮廓或近似的传动关系进行加工而产生的误差。加工原理误差多出现于螺纹、齿轮、复杂曲面加工中。机床的调整误差是指由于调整不准确而产生的误差。夹具的误差主要指:定位元件、刀具导向元件、分度机构、夹具体等的制造误差;夹具装配后,以上各种元件工作面间的相对尺寸误差;夹具在使用过程中工作表面的磨损。为进一步提高静压轴承的动态刚性,机床静压轴承正向提高供油压力方向发展,以适用于粗精加工的需要。南京锯片磨床动静压主轴
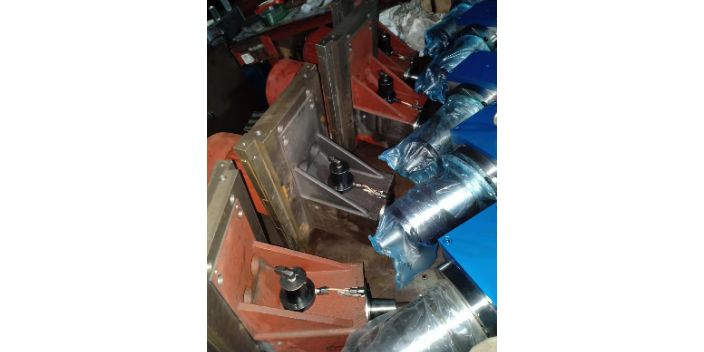
圆柱滚子轴承类别:四列轴承,四列圆柱滚子轴承主要用于冷、热轧机、开坯机等轧钢机机械上,轴承为分离式结构,轴承套圈和滚动体组件可方便地分离,因此,轴承的清洗、检查或安装拆装均很方便。FC型,,FC型轴承由两个外圈和一个内圈组成,每个外圈的两侧有挡边中间有中挡边,内圈无挡边。FCD型,FCD型轴承实际上是由两个NN型轴承组合而成。FC型和FCD型轴承可以允许轴相对轴承座之间在轴向产生两个方向的位移。因此,此类结构适于作游动端轴承。该类型轴承的保持架多采用车制实体13:58 。液体静压磨头厂商能用动压轴承应尽量用动压轴承,只有动压轴承不能满足要求时才用静压轴承。
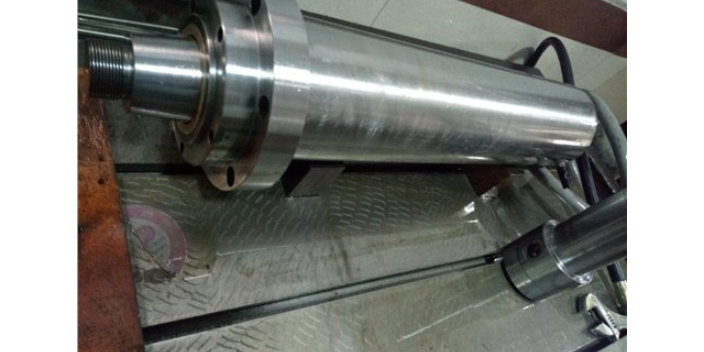
静压主轴检查方法各种机械伤痕,诸如磨伤,划伤、压伤、碰伤等,都会造成轴承安装不良,引起偏载和应力集中,造成旋转精度和使用寿命的下降。锈蚀、黑皮和麻点,后两种是容易储存水分和污物的缺陷,较容易发展成锈蚀。而锈蚀则是导致安装不良、早期磨损和疲劳的污染源,严重的锈蚀会使轴承报废。各种裂纹,诸如原材料裂纹,锻造裂纹、热处理裂纹和磨削裂纹等,这些裂纹在以后轴承的运转过程中,将成为应力集中源而迅速扩大,造成轴承破裂,对轴承寿命和工作安全性影响极大。事实上,对于重要用途的轴承,轴承厂已对其组成零件进行100%磁力或射线探伤检查。
滚动轴承的分类:推力滚子轴承,推力滚子轴承用于承受轴向载荷为主的轴.经向联合载荷,但经向载荷不得超过轴向载荷的55%。与其它推力滚子轴承相比,此种轴承摩擦因数较低,转速较高,并具有调心能力。29000型轴承的滚子为非对称型球面滚子,能减小棍子和滚道在工作中的相对滑动,并且滚子长.直径大,滚子数量多载荷容量大,通常采用油润滑,个别低速情况可用脂润滑。在设计选型时,应优先选用。 主要应用于水力发电机, 起重机吊钩,等等 。圆柱滚子轴承,圆柱滚子轴承的滚子通常由一个轴承套圈的两个挡边引导,保持架.滚子和引导套圈组成一组合件,可与另一个轴承套圈分离,属于可分离轴承。此种轴承安装,拆卸比较方便,尤其是当要求内外圈与轴.壳体都是过盈配合时更显示优点。此类轴承一般只用于承受径向载荷,只有内外圈均带挡边的单列轴承可承受较小的定常轴向载荷或较大的间歇轴向载荷。 静压主轴的润滑系统由油箱,润滑泵,过滤器,溢流阀,安全阀,蓄能器,节流器,油腔,封油面等。
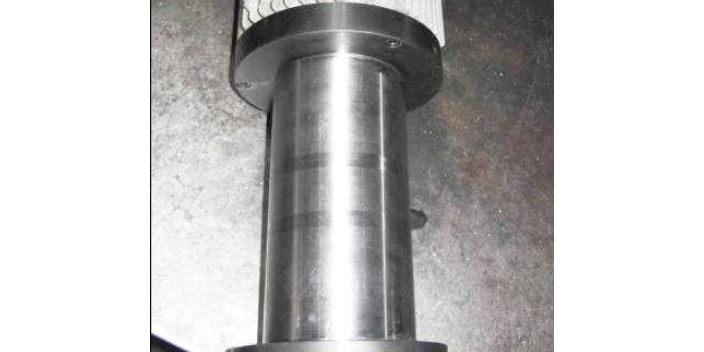
设计液体静压轴承时应根据要求性能进行优化,如要求承载能力很大,油膜刚度很大,位移很小,功耗很少等。为增大轴承的动压效应和减少流量,液体静压轴承的封油面宜适当取宽些;为提高轴承的油膜刚度,轴承间隙宜适当取小些;轴承的温升、流量与供油压力成正比,泵功耗与供油压力的平方成正比,故在满足承载能力的前提下供油压力不宜过高。设计状态下的油腔压力与供油压力之比称为压力比。它是影响轴承性能的重要参数,可根据对承载能力、油膜刚度和位移等不同要求选取。按设计状态下油膜刚度很大的原则选取时,压力比为:毛细管节流器0.5,小孔节流器 0.586。润滑油粘度应根据轴承的摩擦功耗和泵功耗之和为很小的原则选取。对于中等以下速度的轴承,摩擦功耗与泵功耗之比为1~3时,总功耗为很小。相反地,油粘度低,润滑油膜厚度不好,则缩短。武汉静压气浮主轴报价
液体静压轴承在满足承载能力的前提下供油压力不宜过高。南京锯片磨床动静压主轴
静压主轴的旋转精度是指装配后,在无载荷、低速转动条件下,主轴前端安装工件或刀具部位的径向和轴向跳动。旋转精度取决于主轴、轴承、箱体孔等的制造、装配和调整精度。主轴组件运转时,因各相对运动处的摩擦发热,切削区的切削热等使主轴组件的温度升高,形状尺寸和位置发生变化,造成主轴部件的所谓热变形,主轴热变形可引起轴承间隙变化,润滑油温度升高后会使黏度降低,这些变化都会影响主轴组件的工作性能,降低加工精度。因此,各种类型机床对温升都有一定限制。如高精度机床,连续运转下的允许温升为8~10℃,精密机床为15~20℃。普通机床为30~40℃。南京锯片磨床动静压主轴
上一篇: 北京液体静压主轴联系电话
下一篇: 济南定制液压站公司