江门压铸零件加工管理软件开发
机加工企业如何通过管理软件系统实现数字化转型?产品设计数字化。机加工企业在产品设计方面也可以实现数字化。通过使用CAD(计算机辅助设计)、CAE(计算机辅助工程)等软件,企业可以优化产品设计、分析和验证过程,提高产品的设计质量和效率。此外,数字化设计还可以实现快速原型制作,缩短产品上市周期,提高市场竞争力。数字化供应链管理。机加工企业在供应链管理方面也可以通过管理软件系统实现数字化转型。通过整合供应链上下游信息,实现供需信息的即时传递和共享,企业可以优化供应链管理流程,降低库存成本,提高供应链的灵活性和响应速度。同时,管理软件系统还可以提供供应商管理、采购管理、物流管理等功能,帮助企业实现供应链的全i面数字化管理。零件加工管理软件的应用案例。江门压铸零件加工管理软件开发
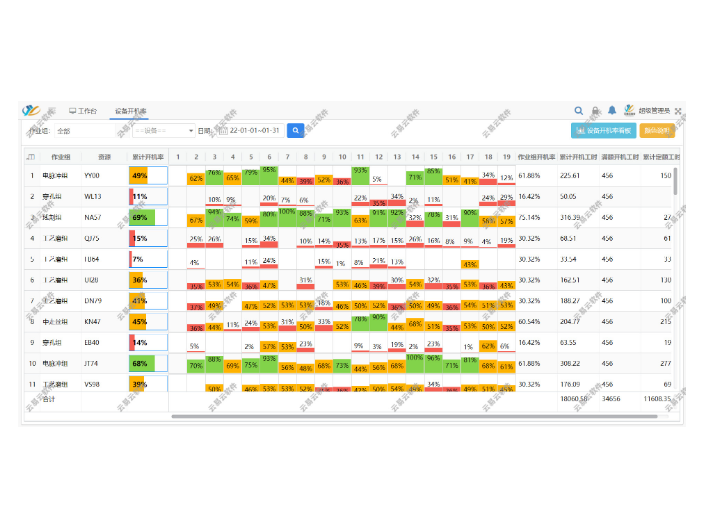
零件批量生产的精益化管理策略价值流分析。首先,我们需要对零件生产的整个价值流进行分析,找出生产过程中的浪费环节,如过多的搬运、等待、库存等。通过绘制价值流程图,我们可以清晰地看到生产过程中的问题,为后续的改进提供方向。小批量生产与单件流与传统的大批量生产相比,小批量生产和单件流更能体现精益化管理的思想。通过减少批量中的数量,我们可以降低库存,减少等待时间,提高生产效率。同时,单件流的生产方式可以确保每个工序都在不停地进行,减少停工和等待,进一步提高生产效率。江门压铸零件加工管理软件开发零件加工管理软件中的工艺优化建议功能,帮助企业不断改进加工工艺和提高生产效率。
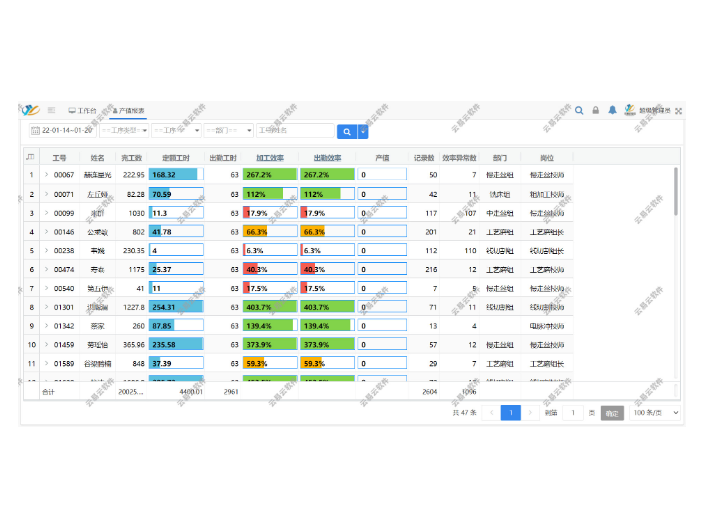
零件加工管理软件有助于提升企业的客户服务水平。软件可以实时跟踪客户订单的生产进度,并将信息及时反馈给客户。客户可以通过在线平台随时查询自己订单的状态,了解零件的加工进度、预计交货时间等信息。这不仅提高了客户的满意度,还增强了客户对企业的信任。此外,软件还可以帮助企业更好地管理客户需求。当客户提出变更订单要求时,软件可以快速响应,调整生产计划,确保满足客户的新需求。通过提升客户服务水平,零件加工管理软件为企业赢得了更多的客户的资源和市场份额。
零件加工管理软件是企业数字化转型的重要支撑。在数字化时代,企业需要将传统的生产管理模式转变为数字化、智能化的管理模式。零件加工管理软件通过整合企业内部的各种信息系统,实现了数据的互联互通和共享。它可以将生产数据与企业的其他业务数据进行融合分析,为企业的决策提供更多面、更准确的依据。同时,软件还可以与物联网、大数据、人工智能等新兴技术相结合,为企业带来更多的创新应用。例如,通过与物联网技术结合,软件可以实现设备的远程监控和预测性维护;通过与大数据分析技术结合,软件可以挖掘出更多的生产优化潜力。通过助力企业数字化转型,零件加工管理软件为企业的未来发展奠定了坚实的基础。零件加工管理软件是一款用于优化和跟踪零件制造过程的应用程序。
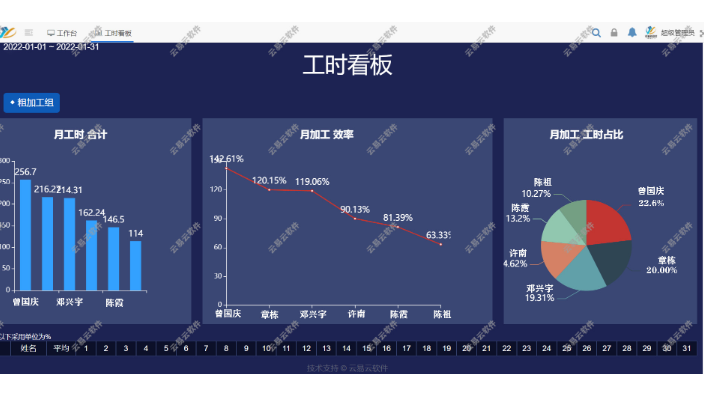
机加工企业管理软件系统常见问题及解决方案。解决方案。提高系统集成度,实现信息共享针对系统集成度低的问题,机加工企业可以通过引入先进的集成技术和中间件,将各个子系统紧密地连接在一起,实现信息的实时共享。这样,企业可以更加准确地掌握生产、库存、财务等各方面的信息,为决策提供有力支持。加强数据分析能力,提供决策支持为了提高数据分析能力,机加工企业可以引入先进的数据挖掘和人工智能技术,对系统中的数据进行深入分析和挖掘。同时,企业还可以建立数据分析团队,对分析结果进行解读和应用,为企业的决策提供有力支持。优化操作界面,提升用户体验为了提高用户体验,机加工企业可以优化管理软件系统的操作界面,使其更加简洁、直观。同时,企业还可以提供详细的操作指南和培训支持,帮助员工快速掌握系统的使用方法。此外,企业还可以根据员工的反馈意见不断改进系统,提升用户体验。通过零件加工管理软件,可以实现对电子零件加工过程的全i面管理和控制,提高零件的质量和可靠性。广东江门智能零件加工管理软件开发
零件加工管理软件可以实时跟踪每个零件的生产进度,帮助管理人员了解每个环节的生产状况。江门压铸零件加工管理软件开发
在制造业的浪潮中,零件批量生产作为产业链的重要一环,其效率和质量直接影响着产品的市场竞争力。然而,如何在保证产量的同时,实现精益化管理,减少浪费,提高生产效率,成为众多企业关注的焦点。下面,就跟着我们云易云软件一起探讨如何实现零件批量生产的精益化管理。理解精益化管理的核i心。精益化管理,源于丰田生产方式,其核i心思想是通过消除浪费、持续改进、全员参与等方式,实现资源的Z好配置,提高生产效率和产品质量。在零件批量生产中,精益化管理意味着要优化生产流程,减少不必要的等待和搬运,降低库存,提高生产线的灵活性和响应速度。江门压铸零件加工管理软件开发
上一篇: 广东中山口碑好的模具ERP供应商
下一篇: 广东五金加工模具ERP生产制造