福建视觉检测图
定制机器视觉检测随着产品及组件的质量标准面临着越来越严格的法规要求,条形码、二维码的阅读、验证及分级在许多检测过程中变得愈发重要。条码技术是信息数据自动识别、输入的重要方法和手段。现已应用到了商业、工业、交通运输业、邮电通讯业、物流、医疗卫生等国民经济各行各业。南京熙岳智能科技有限公司利用高速CCD摄像机得到条码的图像,通过几何转换,滤波去噪,阈值处理等有效的图像处理和快速模式识别方法,结合优化设计的条码码制数据库实现了对一些包裹、印刷品表面的条形码、二维码、字符和流水线物品条码的快速、精确识读。同时,通过识别技术对数据进行采集、输出,使得采集和输出的数据更为精确。木材的缺陷的数量和位置,包括碎片、裂纹、或其他缺陷,决定了木材的等级。福建视觉检测图
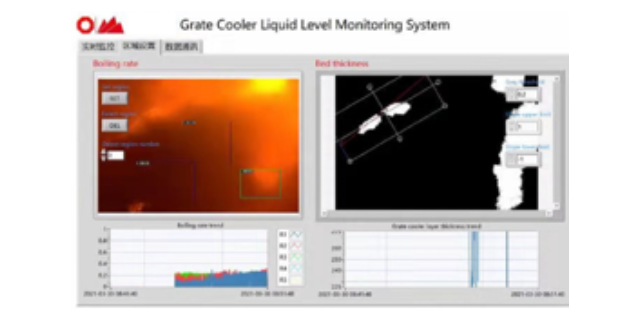
机器视觉检测采用条码质量追溯系统后,工作更简单、方便、准确和快捷。通过数据的采集、管理、检索、存档和统计实时化,质量信息动态地反映生产现状使生产管理者能及时、准确、详细地了解生产情况。产品的自我辨别也是企业保护自己的一种方式,可以防止假冒产品损坏企业声誉。南京熙岳智能追踪系统提高了企业的质量及管理水平,将为企业的决策、管理带来显赫的效益。手工操作已越来越不适应新形势下的现代化管理的要求,计算机技术和条码技术引入生产产品追溯系统领域,已成为必然趋势。例如原来生产质量只能进行现场产品追溯系统,如果产成品出库以后则无法继续追溯其产品的质量情况,各工序生产者,质检责任人等。而现代化的管理要求企业能够为客户提供更多的信息和个性化的服务。广东视觉检测专业随着计算机技术的发展;出现了基于机器视觉技术的表面缺陷检测技术。
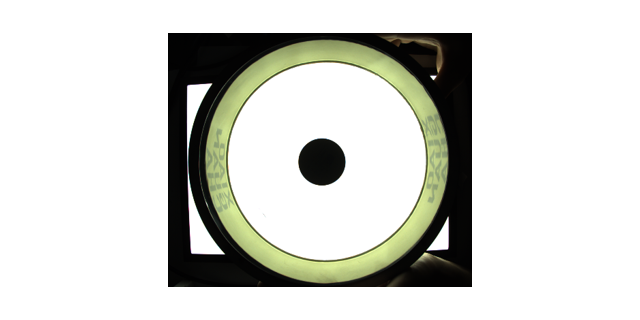
定制机器视觉检测服务在当前大批量工业自动生产过程中,用人工检查产品质量效率过低且精度不高;和其他一些人工视觉检测难以满足要求的场合,表面瑕疵在线检测系统正在迅速取代人工视觉检测。事实上,也正因如此,在世界上现代自动化生产过程中表面瑕疵在线检测系统已广泛应用于带钢、薄膜、金属、纸张、无纺布、玻璃等领域。南京熙岳智能科技有限公司可以定制表面瑕疵在线检测设备。表面瑕疵在线检测系统凝聚了机器视觉领域的多项先进技术应用,并融入了多项创新的检测理念,既可以和现有生产线无缝对接实时在线检测,也可以离线进行检测,在对材料表面的瑕疵以及半透明材料内部瑕疵进行快速检测的同时能够直观的给予生产数据报告反馈,检测精确、稳定、快速、可大幅度提高生产的柔性及自动化程度以提高生产效率,且易于实现信息集成。
光源是机器视觉系统中不可缺少的一部分,在机器视觉缺陷检测中光源的选择非常重要。不同类型的外观缺陷检测有不同的光源方案。例如,多角度和多光谱光源可以用于反射和不规则物体。对于大面积、宽视场的样品检测,条形光源和背光源是优先光源;对于磨砂材料的表面缺陷,可以使用方向性好的光源;对于一些需要多次拍摄且有速度要求的样品,需要使用高亮度光源。只有选择合适的光源,才能更高效地面对不同缺陷的需求。接下来,我们来看看光源在机器视觉检测中的应用。嵌入式技术将用于实现图像处理和深度学习算法的AI模块集成至工业相机,实现边缘智能。
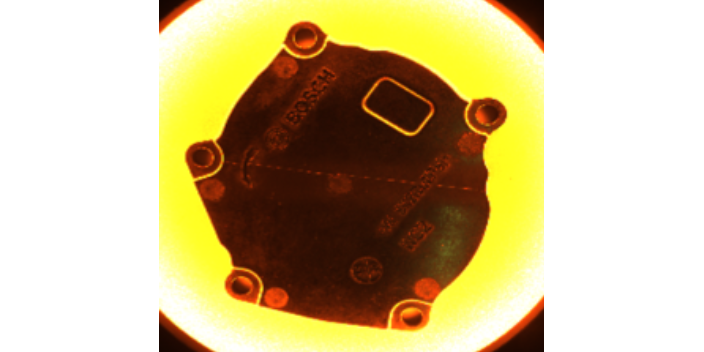
工业机器视觉系统的工作过程主要如下:1.当传感器检测到被检测物体靠近摄像机的拍摄中心时,向图像采集卡发送触发脉冲;2.图像采集卡根据设定的程序和延时向照明系统和摄像头发送启动脉冲。3.向相机发送启动脉冲,相机结束当前拍摄并开始新的拍摄,或者相机在启动脉冲到来之前处于等待状态,在检测到启动脉冲后启动,并在开始新的拍摄之前打开曝光部件(曝光时间是预先设定的);另一个启动脉冲发送给光源,光源的开启时间需要与相机的曝光时间相匹配;相机扫描并输出图像;4.图像采集卡接收信号并通过A/D转换将模拟信号数字化,或者直接接收摄像头数字化的数字视频数据;5.图像采集卡将数字图像存储在计算机的存储器中;6.计算机对图像进行处理、分析和识别,得到检测结果;7.处理结果控制装配线的动作,定位装配线,校正运动误差等。定制机器视觉检测服务机器视觉识别功能要求准确性和精度。浙江aoi视觉检测
饮料分拣与色选、液体检测,生产日期、保质期字符识别;灌装线上空瓶破损、洁净检测等。福建视觉检测图
机器视觉系统的应用,提高了装备的智能化、自动化水平、使用效率和可靠性等性能。为了适应现今这个发展越来越快的社会,机器视觉检测技术是必不可少的。表面检测设备机器视觉系统相对于人工或传统机械方式而言,具有速度快、精度高、准确性高等一系列优点。随着工业现代化的发展,机器视觉检测已经广泛应用于各大领域,为企业及用户提供更优的产品品质及完美解决方案。如何避免此类问题进行质量控制一直是生产企业面临的比较大问题,南京熙岳智能科技有限公司的机器视觉检测技术在工业生产上的应用就完美地解决的这个难题。福建视觉检测图
上一篇: 湖南自动化视觉检测设备
下一篇: 浙江ccd视觉检测机