日照壳体转向器类型
从而可避免因浇口套与压室内径不同轴而造成冲头卡死或磨损严重的问题,且浇口套的壁厚不能太薄。浇口套的长度一般应小于压射冲头的送出引程,以便涂料从压室中脱出。②压室与浇口套的内孔,在热处理后应精磨,再沿轴线方向进行研磨,其表面粗糙≤μm。③分流器与形成涂料的凹腔,其凹入深度等于横浇道深度,其直径配浇口套内径,沿脱模方向有5°斜度。当采用涂导入式直浇道时,因缩短了压室有效长度的容积,可提高压室的充满度。3、内浇口①金属液入型后不应立即封闭分型面,溢流槽和排气槽不宜正面冲击型芯。金属液入型后的流向尽可能沿铸入的肋筋和散热片,由厚壁处想薄壁处填充等。②选择内浇口位置时,尽可能使金属液流程很短。采用多股内浇口时,要防止入型后几股金属液汇合、相互冲击,从而产生涡流包气和氧化夹杂等缺陷。③薄壁件的内浇口厚件要适当小些,以保证必要的填充速度,内浇口的设置应便于切除,且不使铸件本体有缺损(吃肉)。(4)溢流槽①溢流槽要便于从铸件上去除,并尽量不损伤铸件本体。②溢流槽上开设排气槽时,需注意溢流口的位置,避免过早阻塞排气槽,使排气槽不起作用。③不应在同一个溢流槽上开设几个溢流口或开设一个很宽很厚的溢流口。结构紧凑:这种转向器主要由齿轮和齿条组成,结构相对简单、紧凑。日照壳体转向器类型
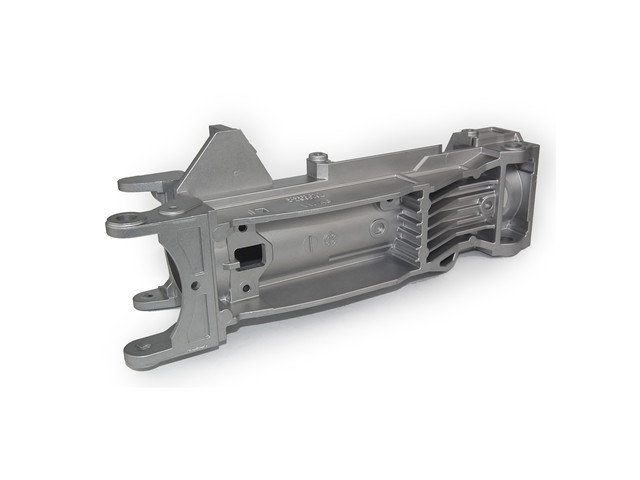
不同厂商的设计加工能力参差不齐,设备也不同。从模具设计和制造过程开始,我们分解其中设计的步骤,逐层剥离复杂的模具,并了解压铸模具的真正成本在哪里。例如,通过积极的核算,了解模具工厂的利润和盈利能力。压铸模具的一般结构可分为模具框架(模具底座),模具芯(模具芯)和标准配件,例如导柱,导套,气缸,油管等。这些是压铸模具的基本组件。如果模具的精度较高,则需要其他零件。压铸模具是成本核算中相对困难的部分,因为涉及的零件类型很多,并且不同处理技术的相应成本也不同;根据零件的不同类型和设计要求,压铸模具的设计差异很大。例如是否需要真空;是否有滑块;或者需要将其应用到大型压铸机上,因此模具的尺寸相对较大。这些差异导致压铸模具设计和加工的差异。另外,型芯的材料选择直接影响模具的使用寿命。杭州转向器铸铝壳体使用寿命长:由于钢球的滚动摩擦代替了部分滑动摩擦,减少了部件之间的磨损。

用3Cr2W8V作压铸模材料,65%是热疲劳,15%是开裂,6%是磨耗,4%是冲蚀失效。:热疲劳裂纹是压铸模常见的失效形式,占失效比例大。压铸过程中压铸模在300~8000C的热循环及脱模剂导致的拉应力与压应力交变循环,反复经受急冷、急热所造成的热应力,导致在型腔表面或内部热应力集中处逐渐产生微裂纹,其形貌多数呈现网状,称龟裂,也有呈放射状。热应力使热疲劳裂纹继续扩展成宏观裂纹。从而导致压铸模失效。热疲劳裂纹是热循环应力、拉伸应力和塑性应变共同作用而产生的。塑性应变促进裂纹的形成,拉伸应力促进裂纹的扩展与延伸。从微观分析,热疲劳裂纹在晶界碳化物、夹杂物集中区萌生,应选钢质洁净、显微组织均匀的高质量的模具钢有较高的热疲劳抗力。:整体脆性开裂是由于偶然的机械过载或热过载而导致压铸模灾难性断裂。材料断裂时所达到的应力值一般都远低于材料的理论强度,由于微裂纹的存在,受力后将引起应力集中,使裂纹顶部的应力比平均应力高得多。压铸模脆性开裂引起的原因很多,而材料的塑韧性是箱对应的非常重要的力学性能。模具钢中夹杂物减少,韧性明显提高,在生产中整体脆裂的情况较少发生。熔融的金属液以高压、高速进入型腔。
设计灵活性:锌合金压铸模具能够适应复杂多变的产品设计需求,从简单的几何形状到复杂的内部结构,都能轻松应对。环保与可持续性:锌合金材料可回收再利用,降低了环境污染,符合绿色制造的发展趋势。三、锌合金压铸模具的行业应用实例锌合金压铸模具在多个行业中发挥着至关重要的作用,包括但不限于:汽车制造业:用于制造发动机部件、底盘零件、内饰件等,提高车辆的安全性和舒适性。电子消费品:用于制造手机外壳、平板电脑边框、智能家居设备等,提升产品的美观度和耐用性。医疗器械:用于制造手术器械、医疗设备外壳等,确保医疗产品的精确度和安全性。航空航天:用于制造飞机零部件、卫星组件等,满足航空航天领域对轻量化、强度高材料的需求。四、锌合金压铸模具的未来发展趋势随着智能制造和工业,锌合金压铸模具行业正迎来新的发展机遇。未来,锌合金压铸模具将更加注重技术创新和智能化发展,如采用数字化设计、智能监测、自动化生产等技术手段,提高模具的制造精度和生产效率,降低生产成本,提升企业的竞争力。同时,随着环保意识的增强,锌合金压铸模具将更加注重材料的可回收性和生产过程的环境友好性,推动绿色制造的发展。综上所述。 操作手感舒适:钢球在循环通道内滚动,使转向过程中的摩擦力较小,且力的传递均匀。

铝压铸模具制作工艺流程:一、铝压铸模具设计:分为产品拆分、流道设计、滑块、顶针、排气、排渣设计等等;这个需要模具设计师具备充分的从业经验以及对产品的熟悉,这样设计出来的铝压铸模具不管是使用寿命还是压铸成型的产品都能有好的效果;二、设计出图:把铝压铸模具的各个部件和配件逐一出图,首先是3D图纸,其次是2D图纸,出图后首先设计要审核,其次是模具部门主管以及项目对应工程师、业务审图,确保铝压铸模具的顺利制作和生产;三、铝压铸模具加工:模具加工分为模架加工、模仁(模芯)加工、顶针、滑块等等配件加工,除此之外还需借助火花机、铣床、磨床、CNC、热处理等等模具制作设备进行加工;四、铝压铸模具的组装:这个版块则需要前面的工序都顺利完成,各种配件到位的情况下进行,一般是由负责此套模具的钳工负责,这个需要钳工对此模具非常熟悉,以及具备一定经验,懂图纸、装配技术好、懂各种模具制作机械,不然在装配的情况下不能单独应对,具备丰富经验的钳工师傅往往能单独面对各种问题组装好一套模具。那么你知道在压铸模具加工工艺过程中影响压力的因素有哪些?压铸工艺就是利用机器、模具和合金等三大要素,将压力、速度及时间统一的过程。工作稳定:液压系统一旦建立起工作压力,就能够稳定地提供助力。常州机械式转向器分类
上海神富机械科技有限公司为您提供转向器,有想法的可以来电咨询!日照壳体转向器类型
或碳氮共渗)_精磨或精研_装配。对H13钢采用高温淬火、双重淬火、控制冷却速度淬火、深冷处理等,从而改善模具性能,提高模具寿命。4、压铸模表面强化处理对压铸模具进行表面处理是延长模具寿命的有效、经济的方法。通过调整一般热处理工艺改善钢的强度和韧性。采用不同的表面强化处理工艺,以适宜的心部性能相配合,可赋予模具表面以高硬度、耐磨耐蚀、抗咬合和低摩擦系数等许多优良性能,使模具寿命提高几倍甚至几十倍。模具表面强化主要有3类:①不改变表面化学成分,有激光相变硬化等;②改变表面化学成分,渗氮等;③表面形成覆盖层,气相沉积技术处理等。5、优化模具设计及压铸工艺减少模具上尖角、拐角的地方,合理使用材料,规范加工和热处理工艺。模具的氮化处理要控制模具的表面硬度HV,>600,氮化层深度达到0.12~0.2mm。正确的预热模具,优化模具以改进内部冷却,使模具获得均匀热平衡效果,使模具维护稳定较低的温度,合理喷涂涂层,涂层对延缓热疲劳裂纹有重要意义,提高模具寿命和效益。模具压力加工是机械制造的重要组成部分,而模具的水平、质量和寿命则与模具表面强化技术息息相关。压铸模的工作条件极为复杂和恶劣,影响模具失效的主要是热疲劳。日照壳体转向器类型
上一篇: 徐州壳体转向器壳体模具
下一篇: 重庆转向器厂家